PHARMA MACHINERY & EQUIPMENTS: BY PIYUSH TRIPATHI
MANUFACTURING
Manufacturing is the use of machines, tools and labor to make things for use or sale. The term may refer to a range of human activity, from handicraft to high tech, but is most commonly applied to industrial production, in which raw materials are transformed into finished goods on a large scale. Such finished goods may be used for manufacturing other, more complex products, such as household appliances or automobiles, or sold to wholesalers, who in turn sell them to retailers, who then sell them to end users - the "consumers".
Manufacturing takes place under all types of economic systems. In a free market economy, manufacturing is usually directed toward the mass production of products for sale to consumers at a profit. In a collectivist economy, manufacturing is more frequently directed by the state to supply a centrally planned economy. In free market economies, manufacturing occurs under some degree of government regulation.
Modern manufacturing includes all intermediate processes required for the production and integration of a product's components. Some industries, such as semiconductor and steel manufacturers use the term fabrication instead. The manufacturing sector is closely connected with engineering and industrial design. Pharmaceutical machinery manufactures have understood the concept behind the process involvement for development of drug, machinery are developed as per client process requirement. Need for such development required in-depth study and monitoring process requirements of clients. Machinery manufactures updated their facilities by latest automated machinery for manufacturing parts, in addition to this there are also other visible trends that can explain committed interest of Indian machinery manufacturers further:
- Manufactures are going for CNC machine to get quality output
- Use of efficient and modern gadgets in the machine, like, VFD, PLC etc.
- Quality approvals and Trademarks, getting ISO approval and international certificate approval for quality manufacturing are also a part of dedication.
- To adapt and implement prototype machines are imported by manufactures.
- Tie-up & Collaboration for technology transfer with international manufactures.
- Expanding high tech facility to meet rising global demand.
Indian Pharma Machinery Manufacturers Association (IPMMA) is also established to work as entrepreneur’s team and also sets technological fairs and international and domestic meet providing a platform for B to B meets and bringing client and manufacture directly in touch with each other and working for mutual benefit.
PHARMACEUTICAL MACHINERY SEGMENT
Industrial segment specially pharmaceutical process and packaging sector have adopted modern means of process evolvement, manufactures have upgraded and adapted modern means of process plant development for providing controlled economical and efficient setups to cope up with the up coming trend and technological advancements. In many production plants, pharmaceutical manufacturers have developed a high degree of automation. Milling and micronizing machines, which pulverize substances into extremely fine particles, are used to reduce bulk chemicals to the required size. These finished chemicals are combined and processed further in mixing machines. The mixed ingredients may then be mechanically capsulated, pressed into tablets, or made into solutions. One type of machine, for example, automatically fills, seals, and stamps capsules. Other machines fill bottles with capsules, tablets, or liquids, and seal, label, and package the bottles.
At the time of industrialization growth flow in 60’s and 70’s the pharmaceutical industry big or small were forced to imported machines from Europe for their processing and packaging needs. During the phase entrepreneurs, engineers in India realized the need for development in the sector for better improvement and meeting requirements of the fastest growing Industry Pharmaceutical process and packing. After the declaration of industrial policies in the mid 70's Indian government introduced very high import duties and restrictive import licensing policies. This resulted in a spark in the Indian engineers to prove their excellence as enterprises to manufacture machines locally. Engineers had the skills and now the support of industry and associations were form to cater the domestic market for better improvement as perhaps the only route for the pharmaceutical industry to enhance production and cater to the growing demands of the domestic market.
With this big a size of the industry a proper setup development plan and skill to cater the need was inevitable. Pharmaceutical Industry grew at the most fastest rate in India for its mineral rich resources, ore availability, raw material power house of such basic ingredients which were cheaply available in local market strengthen the growth. To support the industry Pharmaceutical Machinery Manufactures also upgraded themselves and adapted to a marketing plan. To ensure proper flow and meeting technological upgrades manufactures had to plan a proper strategy for not only meeting requirements but also giving technological upgrade the equipments for faster and efficient working.
DOMESTIC MANUFACTURING CHALLENGES
The machinery manufacturing industry, like all international manufacturers, continues to evolve. Domestic and foreign competition has required the industry to adopt new technologies and techniques to lower costs and raise the productivity of its workforce. For example, using high-technology production techniques, including robots, computers, and programmable equipment results in productivity gains and helps to maximize the use of available equipment and workers. Increasing technology and automation also reduces the number of unskilled workers needed in the production process.
Pressures to reduce costs and maximize profits have also caused manufacturers in the industry to adopt new business practices. One example is the practice of contracting out support functions, such as janitorial and security jobs, and increasingly some administrative services and warehouse and shipping jobs. Rather than employ workers directly for these jobs, a manufacturer will often contract with another company that specializes in providing these services. This practice reduces costs by forcing service providers to compete for the work, allows manufacturers to focus on their core design and production activities, and increases manufacturers’ flexibility by letting them add and subtract contract workers more easily than they could hire and fire employees.
These changes have had a profound effect on the machinery manufacturing workforce. By automating many of the production processes and outsourcing many of the administrative and support functions, it has reduced the need for many less skilled workers and increased the skill level required for the remaining workers. These changes are allowing the industry to remain competitive and meet the demand for machinery that other industries rely on.
One of the greater challenge faced is specialization in restricted field of work to set up a work force which requires, Engineers specialize in a particular facet of design. Mechanical engineers design the moving parts of the machine, such as the gears, levers, and pistons in engine and hydraulic systems. They also direct the work of mechanical engineering technicians, who run tests on materials and parts before they are assembled into the final product. For machines with complicated electric or electronic systems, electrical and electronics engineers also assist in the design and testing process. Industrial engineers determine how best to allocate the resources of the factory—both workers and equipment—for optimal production. Once a design is finished and simulation testing complete, mechanical drafters creates the plans that production workers use in the assembly of the machine. They provide specifications and diagrams for each part required, as well as assembly instructions for the final product. Computer control programmers and operators manage the automatic metalworking machines that can mass produce individual parts. They also write programs based upon the specifications of the part that defines what operation the machine should perform. Machinists produce precision parts that require particular skill or that are needed in quantities too small to require the use of automated machinery. Welding, soldering, and brazing workers operate machines that join two or more pieces of metal together; they may also weld manually as well.
Once all of the parts have been made, it is the responsibility of assemblers and fabricators to put them all together to finish the product. Some assemblers specialize in one particular stage of the process, while others, such as team assemblers, work as a group and may contribute to an entire subassembly process. While there has been increased automation of the assembly process, many parts of the products still have to be put together and fastened by hand. When assembly is complete, painting workers apply paint or a protective coating to the exterior of the machine.
While quality control is a responsibility of all production workers, it is the primary focus of inspectors, testers, samplers, and weighers. These workers monitor the entire production stage, making sure that individual parts, as well as the finished product, meet the standards set by the company.
In addition to production-specific occupations, this industry has various managers and administrative support personnel to handle functions such as human relations, accounting, and general management. The sales function for many companies is increasingly important. Sales representatives and sales engineers often work together to market the company’s machines to potential buyers, demonstrating how the machine may reduce costs or increase sales. They also explain how to operate the machine and answer buyer’s questions. Sales engineers in particular use their technical background to advise clients on how the machine can best be applied in their individual circumstances and to suggest custom designs or modifications to the equipment as needed.
MANAGEMENT ASPECT OF MANUFACTURING
The main factor affecting the level of employment in the machinery manufacturing industry is the high rate of productivity growth. Increases in productivity allow companies to produce more goods with the same number of workers. Even though output in machinery manufacturing is expected to increase significantly, firms are capable to meet the increase through higher productivity of existing workers, rather than by creating new jobs and increasing work force.
A second factor expected to cause some employment declines in machinery manufacturing is the growing number of imported parts. Earlier only raw material was available now finish part machined and finished are also available and raw material suppliers are supplying the same to compete with the competition. This industry is less likely to lose a large part of its output to imports from other countries than some other manufacturing industries. The large size and complexity of many of the types of machinery made by this industry and the relatively skilled workforce it requires is an advantage that many manufacturing industries do not share.
The manufacturing focus in the early-to-mid-2000s was on new and diverse products to meet the individual needs and desires of the market. Companies in 2003 wanted "quick changeover capabilities, flexibility, and fast speeds" more than any other features. Consequently, the industry was expecting continued growth to meet demands for newer and better packaging machinery, replacing older equipment with newer, faster, more efficient, and more automated machines. Trends toward lightweight, individually designed, flexible, and reusable packaging increased demand for the design of machines that could manufacture such packaging.
Demand for machinery is expected to remain strong. Machinery is important for all industries because it boosts their productivity, and advances in technology will make machinery even more efficient and thus more desirable. Demand for machinery is highly sensitive to cyclical swings in the economy, however, causing employment in machinery manufacturing to fluctuate. During periods of economic prosperity, companies invest in new equipment, such as machinery, in order to boost production. When economic growth slows, however, many companies are reluctant to purchase new machinery. These changes in demand cause machinery manufacturers to replace fewer workers who leave or even lay off some workers.
Although overall employment in the machinery manufacturing industry is expected to decline, the outlook for occupations will vary; some will experience larger declines than others, while some will even experience growth instead. Increased automation and more efficient production processes will cause employment declines in assembler and fabricator occupations. Office and administrative support workers will also experience declines as a result of increased automation and contracting out. Employment in professional and management occupations will experience smaller declines relative to other occupations in the industry; engineers in particular will experience very good employment opportunities, as they are responsible for increasing innovation and competitiveness in the industry.
USE OF PROCESS & PACKAGING MACHINERY
Primary use of process and packaging machinery is to elated equipment and it's uses.
BLENDING & MIXING
Blending is to combine or mix so that the constituent parts are indistinguishable from one another and to obtain a mixture of particular character, quality or consistency. Blending machines such as Agitators, Conical blenders, Continuous mixers, Dough mixers, Emulsifiers, Gas, Homogenizers, In line mixers, Meat mixers, Paste mixers, Plough blade, Powder mixers, Ribbon mixers, Solid phase mixers, Viscous product mixers, Z Blade mixers.
GRANULATORS
Current good manufacturing practices increasingly require that product is fully contained during processing to protect operators and environment. Integrated process systems not only offer containment but improved productivity through automation, increased yield and efficient cleaning procedures. The granulation process can be one of the following; Low shear dry granulation, high shear wet granulation and melt granulating. Mixing and granulating can be combined into one machine.
HOMOGENIZERS
Homogenizer is to reduce to particles and disperse throughout a fluid. Inline homogenizers are the ideal solution for continuous processing of emulsions and dispersions.
MILLING & SIEVING
The integration of all types of mills and sieves can be tailored to suit the individual needs. There can be specific applications such as hoist mounted systems and high powder containment levels. Other design options include nitrogen purge systems and CIP systems. Quick change over between products is essential and the application of integrated control systems is needed. There are various types of mills such as toothed colloid, corundum stone and perforated disc mills. Product is loaded via a hopper that can also be fitted with a feed screw, or via a pump. The milling zone is sealed by a single or double-acting mechanical seal, with no dead space. All product contact surfaces should be very easily cleaned with no need for dismantling (CIP). Thorough washing of all static seals during the cleaning process complies with the hygiene standards. In all industrial sectors, demands in terms of flexibility and hygiene management are constantly on the increase.
POWDER HANDLING
Common problems include material blockages where sticky poor flowing materials will not discharge from an IBC. Segregation of blended material is another common problem. Segregation can be caused during the discharge from the IBC. It can also occur after discharge from the IBC when product is allowed to fall through long chutes in free fall, and displaced air from below is forced back up the chute and separates the finer particles from the coarser particles.
PROCESS VESSELS
Processing vessels need to be of a high quality construction and are widely used by the food and processing industries. A selection of sizes, specifications and agitator combinations are available to suit most needs. Stainless steel is used for all fabricated parts to meet industry requirements. Pressurized jackets for heating by steam or water facilitate boiling, cooking, melting, dispersion and mixing of products. Vessels can also be equipped for oil heating or water cooling.
IBC / INDUSTRIAL BULK CONTAINER
Container blending has long been established as the most efficient method of blending granules and powders in the pharmaceutical manufacturing process. Reduced loading and unloading times, reduced cleaning time of both machinery and room, improved containment and batch integrity have established IBC blending as the pharmaceutical industry’s technology of choice.
PROCESS PUMPS
Various types of process pumps can be used depending upon the type of product to be moved between or within the complete process line of the various integrated sub systems. Pumps such as centrifugal, diaphragm, dosing, gear, metering, reciprocation and vacuum can be used. For example, vacuum pumps will be used for powder handling but screw metering drives can be used for more accurate powder movement.
PROCESS CLEANING MACHINES
The cleaning of the process machines will be mainly carried out by CIP (Clean In Place) systems. Depending on the sensitivity of the product being produced, the equipment may be cleaned aseptically and therefore eliminating any possible contamination from outside.
STERILIZING MACHINES
Sterilizing machines can also be called, Autoclaves and Retorts. There three main types of sterilizing system; static, rotary and pilot or laboratory systems.
GENERAL CHARACTERISTICS ARE:-
• Steam-Water sprays mix.
• Top shower for cans and glass jars plus side shower for pouches and trays
• Indirect cooling system by heat exchanger allows water recovery.
• All vessel, pipe work and valves and heat exchanger in stainless steel materials
• Insulated shell with mirror polished stainless steel cladding
• PLC control with modem connection allows remote troubleshooting and servicing
• Process monitoring in the operator interface with complete information of temperature, pressure, time and flow
• Easy product recipe setup with password protected access
• Optimum heat distribution (+/-0,5 ยบC)
• Accurate pressure control (+/- 0,05 bar)
The rotary machines will use inverter drives for accurate control during the sterilizing process. There is also associated equipment such as basket trolleys and automatic loading systems available to fully automate the sterilizing process of product.
PROCESS CONTROL SYSTEMS
Compliance, traceability, consistency, and reliability of measurement data are primary concerns for the pharmaceutical industry. The control system is needed to verify the product quality through measuring, counting, inspection and testing of the manufacturing process. Operator input data; scanning systems and feedback systems are used.
PROCESS AND PACKAGING MACHINERY IN GENERAL
These machine types are very general indeed. Each area or sector of packaging equipment can be expanded upon to reveal the various applications that are available today. As technology advances, packaging machines are becoming more and more advanced to not only meet the current demands but to try and "future proof" the packaging equipment and product development within an organization. This can have a bearing on machine costs plus the interchangeability of operators and training. Packaging machines can be integrated into an existing line to enhance the production output or to reduce the labor and down type to pack the product. From single machine, to small systems or complete lines containing more than one new or existing / reconditioned packaging machine can be installed. Depending on the size of the installation, project process line and packaging machinery are available domestically to withstand & compete with market requirements.
Article by:
Piyush Tripathi
Cell: +91-9824663306
Packing and Labelling of Pharmaceuticals By: Piyush Tripathi
The development and implementation of machinery was responsible for one of the great advances in human history, the industrial revolution. Machinery is critical to the production of much of the Nation’s goods and services because nearly every workplace in every industry uses some form of machinery.
While people never use or even see most of the machinery that makes their lifestyles possible, they use the products it makes every day. The machinery manufacturing industry is comprised of industry segments machinery designed for a particular industry—called special purpose machinery: agriculture, construction, and mining machinery manufacturing; industrial machinery manufacturing; and commercial and service machinery manufacturing. The other segments make machinery used by many different industries—called general purpose machinery: ventilation, heating, air-conditioning, and commercial refrigeration equipment manufacturing; metalworking machinery manufacturing; engine, turbine, and power transmission equipment manufacturing; and other general purpose machinery manufacturing.
Packing and Labeling
The development and implementation of machinery was responsible for one of the great advances in human history, the industrial revolution. Machinery is critical to the production of much of the Nation’s goods and services because nearly every workplace in every industry uses some form of machinery.
While people never use or even see most of the machinery that makes their lifestyles possible, they use the products it makes every day. The machinery manufacturing industry is comprised of industry segments machinery designed for a particular industry—called special purpose machinery: agriculture, construction, and mining machinery manufacturing; industrial machinery manufacturing; and commercial and service machinery manufacturing. The other segments make machinery used by many different industries—called general purpose machinery: ventilation, heating, air-conditioning, and commercial refrigeration equipment manufacturing; metalworking machinery manufacturing; engine, turbine, and power transmission equipment manufacturing; and other general purpose machinery manufacturing.
Grocery bags were known in the 17th cent.; however, it was not until the 19th cent. that practical bag-making machinery was developed. That century saw the emergence of metal cans (1810), setup boxes (1844), folding cartons (1879), and the Owens bottle machine (1899). Early in the 20th cent., marketing-oriented packaging began to evolve and branding, quality, storage and handling, and point-of-sale display became important attributes. By the end of World War II, packaging had become a major medium of advertising and marketing. In recent years, consumer advocates have argued that packages should contain more information on nutrition, unit costs, and contents. The Fair Packaging and Labeling Act of 1966 gave the Food and Drug Administration authority to determine that packages are labeled accurately; the 1990 Nutrition Labeling Act required packages to contain more nutritional information, forcing companies to relabel about 75% of all goods carried by supermarkets. Environmental concerns have led to the passage of state and local laws requiring that some types of packages (notably bottles and cans) be recycled. Manufacturers are attempting to allay further regulation by developing and using packages that cause less damage to the environment.
The Art and science of packing and labeling can be explored as technology of enclosing and protecting product for sale, storage, and distribution. Packing process is a design, evolution, as well as a co-ordinate system of preparing goods for supply, sale, and transport logistics to the end user of the products. Packing is most crucial for sale, product presentation, information, preserves, transportation and most importantly identity of brand.
Labeling or marking is more or less electronic or graphical communication, informative, eye catcher, Brand promotion, means for any product to be sold in the market.
Marketing –
Attractive, fine finished packing and labels can encourage potential buyers to purchase the product. Graphic images, bright contrast color, Physical design have important and constantly evolving phenomenon for several decades. In the run for sale, display, marketing communication and graphic design plays an important roll.
Security –
A Good packing is important for it reduces risk for shipment. Tamper resistance packages can be evident feature to help indicate any tampering. Package embezzle can also be avoided, along with more resistant indicating seals. Authentication seals and security printing can be used to help indicate that the package and contents are not counterfeit. More advanced form of packing also has anti-theft devices, such as dye packs, RFID (Radio-frequency identification) tags, electronic article surveillance tags that can be activated or detected by devices at exit points and require specialized tools to deactivate. Such can prevent not only losses but also an adaptive means of improvised packing.
Containment or agglomeration –
Any product may it be liquid, powder and granular material requires containment. Viz. smaller objects are typically grouped together in one pack for reasons of efficiency. For example, one combined box for mango requires less physical handling the packing them individually.
Portion Control –
Individual Packing or single serving packs, single dosage packing has precise amount of contents to control usage. Commodities packed in bulk (Viz. Salt, Sugar, spices) are packed in more suitable size for individual household usages. This also adds to inventory selling as 1 ltr. Pack of sealed milk, rather then having people bring in their own containers to fill themselves.
Convenience –
Design of packages with features that can add to convenience in handling, storage, opening, distribution, sale, opening, use, dispensing and reuse.
Physical Protection –
Quality packing ensures protection from miss-handlings, wastage, shock, compression, temperature, to preserve the material packed.
Barrier Protection –
Barrier from external agents, and contaminants, is a must. The Crucial factor in design of packing is to prevent product and have extend shelf life. Modified atmosphere or controlled atmospheres are also maintained in some food package, keeping contents clean, fresh, sterile, and safe for intended use.
Information transmission –
Package and label communicate how to use, handle, transport, recycle or dispose the package or product. Food, Pharmaceuticals, Medical, Chemical Products, requires guidelines for usage and information required by governments. Package and label also track and trace purposes of the product.
Industry
In pharmaceutical industry machinery manufacturing have evolved in mid 70's when Indian government introduced very high import duties and restrictive import licensing policies. Engineers had the skills and now the support of industry and associations were form to cater the domestic market for better improvement as perhaps the only route for the pharmaceutical industry to enhance production and cater to the growing demands of the domestic market.
Foreign manufactures had a stronghold on the market but today the Engineering excellence of Indian manufactures had turn table not only to the domestic market but all have proved to the world our capabilities. Indian Pharmaceutical industry stands fifth largest producer of drugs and pharmaceutical after USA, Japan, Europe and China.
Pharmaceutical machinery manufactures have understood the concept behind the process involvement for development of drug, machinery are developed as per client process requirement. Need for such development required in-depth study and monitoring process requirements of clients. Machinery manufactures updated their facilities by latest automated machinery for manufacturing parts, in addition to this there are also other visible trends that can explain committed interest of Indian machinery manufacturers further:
- Manufactures are going for CNC machine to get quality output
- Use of efficient and modern gadgets in the machine, like, VFD, PLC etc.
- Quality approvals and Trademarks, getting ISO approval and international certificate approval for quality manufacturing are also a part of dedication.
- To adapt and implement prototype machines are imported by manufactures.
- Tie-up & Collaboration for technology transfer with international manufactures.
- Expanding high tech facility to meet rising global demand.
Labeling Technology
Packing and labeling technology have evolved from semi-automated process to complex still simpler fully automatic ones. Introduction of automation a use of control systems (such as numerical control, programmable logic control, and other industrial control systems), in concert with other applications of information technology (such as computer-aided technologies [CAD, CAM, CAx]), to control industrial machinery and processes, reducing the need for human intervention. In the scope of industrialization, automation is a step beyond mechanization. Whereas mechanization provided human operators with machinery to assist them with the muscular requirements of work, automation greatly reduces the need for human sensory and mental requirements as well. Processes and systems can also be automated.
Engineers strive to combine automated devices with mathematical and organizational tools to create complex systems for a rapidly expanding range of applications and human activities. Incorporating such complex interfaces specialized hardened computers, referred to as a programmable logic controllers (PLCs), are used along with synchronized flow of inputs from sensors and events with the flow of outputs to be actuated for particular event. Many roles for humans in industrial processes presently lie beyond the scope of automation. Human-level pattern recognition, language recognition, and language production ability are well beyond the capabilities of modern mechanical and computer systems. Tasks requiring subjective assessment or synthesis of complex sensory data, such as scents and sounds, as well as high-level tasks such as strategic planning, currently require human expertise. In many cases, the use of humans is more cost-effective than mechanical approaches even where automation of industrial tasks is possible.
Human-machine interfaces (HMI) or computer human interfaces (CHI), formerly known as man-machine interfaces, are usually employed to communicate with PLCs and other computers, such as entering and monitoring temperatures or pressures for further automated control or emergency response. Service personnel who monitor and control these interfaces are often referred to as stationary engineers.
Manufacturing companies, purpose of automation has increased to reduce costs increase productivity; to broader issues such has increasing quality and flexibility in the manufacturing process. Earlier automation simply increased productivity and reduced cost, moreover costs of automation were high and often could not be recovered by the time entire new manufacturing process replaced the old ones. Unlike today where technology has not only overcome the barrier of cost but also has molded itself as an efficient process means.
Labeling and Labels classification:
• Heat activated adhesives: for example, "in-mold labeling" can be part of blow molding containers and employs heat activated adhesives. Hot melt adhesives are also used.
• Pressure sensitive adhesives (also called PSA or self-stick) are applied with light pressure without activation or heat. PSA labels often have release liners which protect the adhesive and assist label handling.
• Rivets used to attach information plates to industrial equipment
• Shrink wrap for printed shrinkable labels placed over packages and then heated to shrink them.
• Sewing for clothing, tents, mattresses, industrial sacks, etc.
• Wet glue (starch, dextrin, Polyvinyl acetate (PVA or PVAc) is a rubbery synthetic polymer., etc) or water moisten able gummed adhesive
• Yarn or twine for tying on a label
Label type requires process machine, with the label up gradation, machines have also evolved. Labels can be supplied:
• Separately (Cut form)
• On a roll
• On a sheet
Many labels are pre-printed by the manufacturer. Other has printing applied manually or automatically at the time of application. Some labels have protective overcoats, laminates, or tape to cover them after the final print is applied. This is sometimes before application and sometimes after. Labels are often difficult to peel and apply. Most companies use a Label dispenser to speed up this task. Specialized high speed application equipment is available for certain uses. Graphic, color and pictures requires base of ink and base stock color choices commonly conform to the Pantone Matching System (PMS) colors. The system is very dominant in the label printing industry. Additionally specialty inks such as metallic, UV ink, magnetic ink, and more are available. Ink is usually transparent however it can be made opaque. It has been known for certain companies to patent "their own" color. Digital labels use process colors to replicate Pantone solid colors.
Most commonly used applicator sticker machines for high speed application has created brand stickers attached to products to identify as coming from certain company. Mainly used to describe characteristics of the products that are not simple and requires precise explanation for promotion and sale, mainly used in pharmaceutical industry.
Packing development consideration
Packing design and development are often thought as an integral part of product development and process. Development of a component can be a separate process, but must be linked closely with the product to be packaged. Identification of all the requirements, Structural design, marketing, shelf life, quality assurance, logistics, legal, regulatory, graphic design, end-use, environmental, etc. The design criteria time targets, cost constraints and resources need to be established and agreed up on. Package design may take place within a company or with various degree of external packaging engineering, contract engineers, consultants vendor evaluation, independent laboratories, contract packagers, total outsourcing etc. some sort of formal project planning and project management methodology is required for all but the simplest package design and development program. An effective quality management system and verification and validation protocols are mandatory for some type of packaging and recommended for all, for example regulation for an over the counter drug might require the package to be temper evident and child resistant, and these intentionally make the package difficult to open. The intended consumer, however, might be handicapped or elderly and be unable to readily open the package. Meeting all goals is a challenge.
Package development involves consideration for sustainability, environmental responsibility, and applicable environmental and recycling regulation. It may involve a life cycle assessment which considers the material and energy inputs and outputs to the package, the package product, the packing process, the logistics system, waste management. Etc. It is necessary to know the relevant regulatory requirements for point of manufacture, sale and use.
The traditional Three R’s reduce, reuse, and recycle are part of waste hierarchy which may be considered in product and package development.
Packaging Machines
Selecting appropriate packaging machinery includes: technical capabilities, labor requirements, worker safety, maintainability, serviceability, reliability, ability to integrate into the packaging line, capital cost, floor space, flexibility (change-over, materials, etc.), energy usage, quality of outgoing packages, qualifications (for food, pharmaceuticals, etc.), throughput, efficiency, productivity, ergonomics, return on investment, etc.
Packaging machines in pharmaceutical industry are classified in to segments depending on industry for which the functional machinery is required. Companies operating in this sector perform the following principal work cycles.
1) Production procedures common to all types of pharmaceutical forms:
a) Weighing of active principles and excipients;
b) cleaning-sterilization of plant systems and work areas.
2) Production of solid pharmaceutical forms.
3) Production of semi-solid pharmaceutical forms.
4) Production of liquid pharmaceutical forms.
5) Packaging lines for the various pharmaceutical forms.
From warehouse to material handling and general process of weighing followed by Granulate preparation or solution preparation, then division in to various form of process viz. tablet capsule production, Suppository, ointment, cream production to container sterilization, then filling sealing of containers to forming tablet or capsule all the process till final packing of product for safe transport after label all is done either by automated or semi automated machines. This vast range of machinery segment covers most important constituent of product forms which we use very commonly without understanding the process involved behind it.
In many production plants, pharmaceutical manufacturers have developed a high degree of automation. Milling and micronizing machines, which pulverize substances into extremely fine particles, are used to reduce bulk chemicals to the required size. These finished chemicals are combined and processed further in mixing machines. The mixed ingredients may then be mechanically capsulated, pressed into tablets, or made into solutions. One type of machine, for example, automatically fills, seals, and stamps capsules. Other machines fill bottles with capsules, tablets, or liquids, and seal, label, and package the bottles. Demand for machinery is expected to remain strong. Machinery is important for all industries because it boosts their productivity, and advances in technology will make machinery even more efficient and thus more desirable.
Article By:
Piyush Tripathi
Cell: +91-9824663306
PHARMACEUTICAL TECHNOLOGY
The development and implementation of machinery is responsible for one of the great advances in human history, the industrial revolution. Machinery encompasses a vast range of products, ranging from huge industrial turbines costing millions of dollars to the common lawn mower, but all machinery has one common defining feature: it either reduces or eliminates the amount of human work required to accomplish a task. Machinery is critical to the production of much of the Nation’s goods and services because nearly every workplace in every industry uses some form of machinery. From the oil derrick that pumps out oil to the commercial refrigerator in use by your favourite restaurant, machinery is necessary for the way we live today. Thus while people never use or even see most of the machinery that makes their lifestyles possible, they use the products it makes every day.
Most machinery is made of metal, which gives the end product strength and durability, but which necessitates specialized procedures in production. Each part needs to be designed to exacting specifications to ensure proper function of the finished product. Techniques such as forging, stamping, bending, forming, and machining are used to create each piece of metal, thousands of which then need to be welded or assembled together in the largest machines. At each stage of production and assembly, extensive testing takes place to maintain quality control standards. Due to the great variety of machinery produced by industry, firms specialize in designing and producing certain types of equipment for specific applications.
In Early 60's and 70's the pharmaceutical industry big or small were forced to imported machines from Europe for their processing and packaging needs. During the phase entrepreneurs, engineers in India realized the need for development in the sector for better improvement and meeting requirements of the fastest growing Industry Pharmaceutical process and packing. In mid 70's Indian government introduced very high import duties and restrictive import licensing policies. This resulted in a spark in the Indian engineers to prove their excellence as enterprises to manufacture machines locally. Engineers had the skills and now the support of industry and associations were form to cater the domestic market for better improvement as perhaps the only route for the pharmaceutical industry to enhance production and cater to the growing demands of the domestic market.
Foreign manufactures had a stronghold on the market but today the Engineering excellence of Indian manufactures had turn table not only to the domestic market but all have proved to the world our capabilities. Indian Pharmaceutical industry stands fifth largest producer of drugs and pharmaceutical after USA, Japan, Europe and China.
With this big a size of the industry a proper setup development plan and skill to cater the need was inevitable. Pharmaceutical Industry grew at the most fastest rate in India for its mineral rich resources, ore availability, raw material power house of such basic ingredients which were cheaply available in local market strengthen the growth. To support the industry Pharmaceutical Machinery Manufactures also upgraded themselves and adapted to a marketing plan. To ensure proper flow and meeting technological upgrades manufactures had to plan a proper strategy for not only meeting requirements but also giving technological upgrade the equipments for faster and efficient working.
Manufacturing of pharmaceutical products and of chemical and botanical products for medicinal purposes, production sector that includes:
- Test, enhancement and production of active medicinal substances which, due to their therapeutic properties, are used in the manufacture of pharmaceutical products.
- Production of blood derivates for pharmaceutical uses;
- Production of chemically pure sugars;
- Gland processing and production of glandular extracts.
Belonging to the same sector, includes:
- Production of drugs recorded as such in a national register displaying specific component formulation and quantities and possessing a concrete pharmaceutical form which allows them to be assembled; immune serum and other blood components; vaccines, varied packaged/unpackaged medicinal products for retail sale, including homeopathic preparations, dental cavity fillers and cements for bone reconstruction and chemical birth control preparations;
- Production of drug impregnated or coated cotton wool, gauze, dressings, adhesive plasters, etc. production of sterile surgical sutures.
The companies affected by this research display a production cycle which includes the preparation of packaged/unpackaged medicines for retail sale; chemical birth control preparations; test, enhancement and production of active medicinal substances which, due to their therapeutic properties, are used in the manufacture of pharmaceutical products; production of chemically pure sugars.
PHARMACEUTICAL INDUSTRY MANUFACTURING PROCESSES: GENERAL CONSIDERATIONS
Within the pharmaceutical industry, all basic procedures for drug production are performed according to so called GMP (good manufacturing procedures) (official national pharmacopoeia- edition VII). The above procedures are an integral part of the broader Quality Assurance verification system, which brings together all specifications, procedures and structures aimed at assuring that products meet required quality standards. All production facility organizational functions contribute to the verification system’s implementation. The national official pharmacopoeia includes a chapter listing certain useful definitions for the interpretation of the GMP (good manufacturing procedures). Listed hereunder are the definitions relating to the terms “Medicament, Manufacture, Batch, Validation, and Quality Control”.
Medicament:
Any substance or chemical composition displaying curative, prophylactic, diagnostic properties or which allows restoration, modification or correction of organic functions in humans and animals.
Manufacture:
All operations relating to the production of medicaments especially, those relating to the handling of raw materials, mixture preparation, realization of pharmaceutical forms as well as the filling, packaging and labelling of containers.
Batch:
The bulk of a specific medicament manufactured during a single production cycle. The essential feature of a batch is its homogeneity.
Validation:
The documented implementation of a specific verification program aimed at systematically obtaining a product meeting predetermined specifications. The validation process affects manufacturing processes, quality control, plant efficiency and environmental considerations.
Quality Control:
The activities and interventions aimed at ensuring the production of uniform medicament batches to meet predetermined specifications.
The application of quality control rules is targeted to obtaining a product for human or animal administration for curative and/or diagnostic purposes.
Consequently the drug must display low contamination and/or sterility characteristics not required of other products. As a result, employee working conditions are quite unique and aimed at preserving the finished product. A drug production work environment includes areas maintained at various levels of decontamination thanks to ambient air filtering systems, operator protection devices and measures, particularly stringent hygiene standards.
These measures, while ensuring that the drug is free from contaminants, also avoid direct worker contact with pharmacologically active and thus hazardous substances. Daily exposure threshold values (TLV) have been set to ensure worker protection. Threshold values have been arbitrarily set at 1:100 of the lowest pharmacologically active dose (minimum effective dose) bearing in mind that the minimum effective dose was calculated on the basis of conventional drug administration and not resulting from worker exposure.
WORK CYCLE: GENERAL DESCRIPTION
Companies operating in this sector perform the following principal work cycles.
1) Production procedures common to all types of pharmaceutical forms:
a) Weighing of active principles and excipients;
b) cleaning-sterilization of plant systems and work areas.
2) Production of solid pharmaceutical forms.
3) Production of semi-solid pharmaceutical forms.
4) Production of liquid pharmaceutical forms.
5) Packaging lines for the various pharmaceutical forms.
General Drug Production Work Cycle:
Detailed study on process requirements, and corral for equipment requirement, the machinery manufacturing industry is comprised of seven more detailed industrial segments, Three of these make machinery designed for a particular industry—called special purpose machinery: agriculture, construction, and mining machinery manufacturing; industrial machinery manufacturing; and commercial and service machinery manufacturing. The other four segments make machinery used by many different industries—called general purpose machinery: ventilation, heating, air-conditioning, and commercial refrigeration equipment manufacturing; metalworking machinery manufacturing; engine, turbine, and power transmission equipment manufacturing; and other general purpose machinery manufacturing.
Industry segment:
1. Agriculture, construction, and mining machinery manufacturing
2. Metalworking machinery manufacturing
3. Ventilation, heating, air-conditioning, and commercial refrigeration equipment manufacturing
4. Industrial machinery manufacturing
5. Commercial and service industry manufacturing
6. Engine, turbine, and power transmission equipment manufacturing
7. Other general purpose machinery manufacturing
All these segments contribute to the pharmaceutical industry, from construction, metal working, heating, air-conditioning, Industrial machinery, service industry manufacturing, power transmission equipment manufacturing, and general purpose machinery.
The size of an establishment also contributes to how some machinery is produced. Large firms involved in manufacturing machinery tend to have a multistage production process, with separate teams of individuals responsible for design and testing, manufacture of parts, and for assembly of the finished product. Nonetheless, there is considerable interaction between the various types of workers; for example, design offices are often located near the factory floor to promote interaction with production workers. Small establishments, in contrast, may have a handful of workers responsible for the entire production process.
The machinery manufacturing industry continues to evolve. Domestic and foreign competition has required the industry to adopt new technologies and techniques to lower costs and raise the productivity of its workforce. For example, using high-technology production techniques, including robots, computers, and programmable equipment results in productivity gains and helps to maximize the use of available equipment and workers. Increasing technology and automation also reduces the number of unskilled workers needed in the production process.
Pressures to reduce costs and maximize profits have also caused manufacturers in the industry to adopt new business practices. One example is the practice of contracting out support functions, such as janitorial and security jobs, and increasingly some administrative services and warehouse and shipping jobs. Rather than employ workers directly for these jobs, a manufacturer will often contract with another company that specializes in providing these services. This practice reduces costs by forcing service providers to compete for the work, allows manufacturers to focus on their core design and production activities, and increases manufacturers’ flexibility by letting them add and subtract contract workers more easily than they could hire and fire employees.
These changes have had a profound effect on the machinery manufacturing workforce. By automating many of the production processes and outsourcing many of the administrative and support functions, it has reduced the need for many less skilled workers and increased the skill level required for the remaining workers. These changes are allowing the industry to remain competitive and meet the demand for machinery that industries rely on.
Pharmaceutical machinery manufactures have understood the concept behind the process involvement for development of drug, machinery are developed as per client process requirement. Need for such development required in-depth study and monitoring process requirements of clients. Machinery manufactures updated their facilities by latest automated machinery for manufacturing parts, in addition to this there are also other visible trends that can explain committed interest of Indian machinery manufacturers further:
- Manufactures are going for CNC machine to get quality output
- Use of efficient and modern gadgets in the machine, like, VFD, PLC etc.
- Quality approvals and Trademarks, getting ISO approval and international certificate approval for quality manufacturing are also a part of dedication.
- To adapt and implement prototype machines are imported by manufactures.
- Tie-up & Collaboration for technology transfer with international manufactures.
- Expanding high tech facility to meet rising global demand.
Current good manufacturing practice (CGMP) requirements are set forth in quality system regulation. The requirements is part govern the methods used in, and the facilities and controls used for, the design, manufacture, packaging, labeling, storage, installation, and servicing of all finished devices intended for human use. The requirements in this part are intended to ensure that finished devices will be safe and effective and otherwise in compliance with the Federal Food, Drug, and Cosmetic Act (the act). This part establishes basic requirements applicable to manufacturers of finished medical devices. This regulation does not apply to manufacturers of components or parts of finished devices, but such manufacturers are encouraged to use appropriate provisions of this regulation as guidance.
Article By:
Piyush Tripathi
Cell: +91-9824663306
PHARMACEUTICAL MARKETING
Heading of miracle cure with very little potency, is common, genuine non-prescription medications, such as pain relievers or allergy medicine, has now grown to mass marketing of prescription medications which earlier rare, until recently, however. Largely accepted, that since doctors made the selection of drugs, mass marketing was a waste of resources; specific ads targeting the medical profession were thought to be cheaper and just as effective. Sources like ads in professional journals and visits by Medical representatives to doctor’s offices and hospitals. More importantly bringing the upcoming to medical student plays an important part of these efforts.
Pharmaceutical companies are developing processes to influence the people who influence the physicians. There are several channels by which a physician may be influenced, including self-influence through research, peer influence, direct interaction with pharmaceutical companies, patients, and public or private insurance companies. There are also web based instruments that can be used to determine the influencers and buying motives of physicians.
There are a number of firms that specialize in data and analytics for pharmaceutical marketing.
Information source of physicians are, Pharmaceutical information sources as the Physician's Desk Reference and online sources such as PDR.net, as well as via PDAs with applications.
They also rely upon pharmaceutical-branded e-detailing sites, pharmaceutical sales and non-sales representatives, and scholarly literature. Scholarly literature can be in the form of medical journal article reprints, often delivered by sales representatives at their place of employment or at conference exhibitions.
Large size of the sales of Pharmaceutical, the organization, management and effective measurement of the sales force is significant business challenges. Task is broken in to areas like training programs for physicians, force size and structure for sales optimization, call planning and effective sales force. Few Pharmaceutical companies have realized importance of training sales representative on high science alone is not enough especially when most of the products are similar in quality. Thus, now sales representative are trained on relationship selling techniques in addition to medical science and product knowledge, which makes a difference in efficient selling. Especially physicians rely on more and more on specialty sales representation for product information, as they are knowledgeable then primary care representatives.
Physicians are the most important players in pharmaceutical sales. They write the prescriptions that determine which drugs will be used by the patient. Influencing the physician is the key to pharmaceutical Marketing. This is done by a large sales force of representatives explaining benefits, free drug samples, however economic pressures on the industry is causing pharmaceutical companies to rethink the traditional means and sales process to physicians. Due to malpractice, done by large scale companies, physician network associations have adopted new guidelines prohibiting physicians and researchers from accepting gifts from pharmaceutical manufactures. Individual drug samples, left by companies will be distributed through a centralized system, while educational programs, fellowship are now required to be done centrally reviewed and approved.
PHYSICIAN TARGETING
Identification of physician most likely to prescribe a given drug is measured by the number of total prescriptions and new prescriptions per week that the physician writes. This information is collected by commercial vendors. The physicians are then “marked" into groups based on their writing patterns. Higher marked are more aggressively targeted. Pharmaceutical companies use additional information such as:
Prescription Profitability (script),
Accessibility of the physician,
Tendency of the physician to use the pharmaceutical company's drugs,
Effect of managed care formularies on the ability of the physician to prescribe a drug,
How readily the physician adopts new drugs in place of older, established treatments.
The tendency of the physician to use a wide palette of drugs
Influence that physician have on their colleagues.
Hospital prescribed drugs data are not usually available at the physician level, for such analysis, advanced analytic techniques are used to value physicians in the hospital and their sitting. Advanced analysis would chiefly include leadership of the physician, and how much influence does he keeps, among the
Since 1970’s marketing direct to patient has become important. Many patients will inquire or even demand to receive a medication seen or advertised on television.
SALES FORCE SIZE AND STRUCTURE
Companies must decide appropriate size of their sales force needed to sell a particular assortment of drugs to the target region or territory. How many physicians to see? How often to see them? Decide how many representatives to depute to office and group practice and how many to depute to hospital accounts. Customers are divided into different classes; each class is differentiated by their prescription behavior and of course, their business potential.
Public and private insurers affect the writing of prescriptions by physicians through formularies that restrict the number and types of drugs that the insurer will cover. Not only can the insurer affect drug sales by including or excluding a particular drug from a formulary, they can affect sales by tiring, or placing bureaucratic hurdles to prescribing certain drugs.
PHARMACEUTICAL MARKETING AND ADAPTED CONCEPT
We all know that drugs affect the alter health. By their very nature they play a prominent roll in society. The Medicine/drug industry consequently also plays a important role. Chiefly the roll of marketing medicines / drugs rely on :
1. Discovery and development of New drugs/medicines.
2. Rapid and safe development of medicines/drugs in to useful therapeutic tools and
3. Production and Distribution of safe and efficient existing medicines/drugs
The efforts of marketing practitioners to match as closely as possible the marketing mix of their companies with the needs of the consumer has let to the development of a way to thinking known as the marketing concept. The marketing concept states that what seems obvious now, but was not always practiced, that is easier to change the products and activities of the individual manufacturer to fit the market than it is to convince the entire market to use the products and services as the individual marketer prefers them. The marketing concept further requires that all of the resources of the firm to be organized in to a total system aimed at meeting the needs of the customer. Those firms which once prided themselves on their production expertise now find that marketing know how is perhaps more important.
Marketing plays a key role, in directing activities from the manufacture to the patient. And the patient, it should be noted, stands at the peak of the marketing Pyramid. It is characteristics of a patient which determine which goods will be sold or, more correctly which goods are to be produced. Any firm thus strive to direct marketing activities so the right product is sold in right quantity at the right place at right price at the right time.
Marketing Succeeds in basic task, defined to include right product, quantity, place, price and time, it is still theoretically possible for the product to fail a marketable item. The area of failure could be described broadly as communication. The amount of information that must be communicated by the manufacturer is the availability of a product. One does not buy a product that does not exist. The physician is engaged in astounding search, i.e. with knowledge of the needs of patient, he search the characteristics of available products for the patient, for that which most closely approximates the answer to the patient’s problem. The Physician is engaged in this relatively active and educates search process there is a strong possibility that he will not become aware of a given product unless someone has made a formal effort to communicate to him its availability.
PLANNING AS A CONCEPT
If you don’t know where you are going, any road will take you there. Whoever the expression is without marketing mind concept. The Marketing Planning system is designed to help produce dynamic line management tool, not a fat document conceived in an ivory tower, to which no one pays any attention. A market plan is incomplete without hard figures, but figures alone do not make a plan.
Marketing plant is a clear statement of the goals/objectives, the strategy for achieving the objectives and a plan that demonstrates how the strategy will be implemented, also, at the outset, a summary of the business situation as we see it, highlighting the issues. This provides the context for strategy for the reader. It also serves as a useful reminder to the plan of the issues which are supporting the strategic choice. If the issues change, inevitably the strategy and/or implementation plan will also need to be adjusted.
A decision make today about allocating resources is dependent up on an interpretation of a known set of variables covering some of the existing potential futures. Viz.
Customers
Producers
Price
Costs
Production
Technology
Distribution
Competition
Regulations
Managers must have an awareness of these variables, even if they do not have complete information. However, today’s known variables become tomorrow’s unknown, and the only thing certain about tomorrow is that it will be different from today. Thus, the marketing planning process must also consider the possible shape and nature of these variables in the future. This is generally sufficient to make good decisions about the optimal allocation of resources to generate today’s business and make as equally competitive tomorrow’s business.
A Good plan:
- Help in identify and develop the new skills and procedures that will be required in the future the skills and procedures that managers have developed to deal with today’s decisions are rarely adequate for marketing decisions about tomorrow.
- Prepare the company for change so that it can take a commanding lead over those companies that merely react, as business inevitably change, so marketing planning helps the transition from today to tomorrow to be smooth and predictable. Planning for changed circumstances provides the single opportunity to gain significant advantage over the competition. Regulatory requirements, product innovation, new technology, standardized distributing and other relatives all combine to even not companies. Yet, the same factors which account for market changes also provide great opportunities.
- Provide a vehicle for communicating the changes and their effects in an open and non-threatening manner. A common belief is that people resist change only when they are uncertain of the personal effect. When change is shown to be beneficial, it tends to be supported.
- Calculate and reduce the available options to achieve the best chance of success and the least chance of error. There is a little choice when allocating today’s resources and thus, little room for error.
- Provide a method for handling complexity: more often then not a pharmaceutical company serves several markets. There are several groups of people who use or buy each product. Each group of people is subject to change, both in varying direction at different rates. One way of dealing is reacting when forced to, ignoring the complexity and taking the least possible action. It is through evaluating each market, establishing the nature of the changes and deciding on profit potential, that resources can be allocated. Thus, the strategy can be the same, but the local market objectives and how that strategy should be implemented will probably always be different.
- Identify the roll of each department and offers the means to co-ordinate their activities, as with changing markets. Company has national and international markets may have many departments to cater for some activity that meets the needs of these markets. If all these departments are not coordinated and heading in the same directions.
- Ensure that the company is proactive in its approach to acquiring the capabilities in needs, as a company develops, so each of the department evolves, this leads to increase demand upon the resources of time and money. If reactive decisions are made, the resulting demands for plant, equipment, R & D, people, finance, even products, exceed the company’s ability to supply. Result, growth becomes disorderly and wasteful, competitive advantage is forfeited and profits delayed or lost.
Conclusion, of marketing planning is to ensure an orderly and profitable transition from today to the future. If as a manager, you enjoy letting things happen, if things are good enough as they are, or if you like to panic decisions, then marketing planning has no value. If you want to understand control your growth, improve your profits or increase the chances of your company’s survival, then marketing planning is not an option, it is mandatory. Planning is not something apart from the rest of the business. To be successful, it must determine activities and be recognized for what it is by the whole company.
Article By:
Piyush Tripathi
Cell: +91-9824663306
Critique on Pharma Industry
The first Indian pharmaceutical company, Bengal Chemicals and Pharmaceutical Works, which still exists today as one of 5 government-owned drug manufacturers, appeared in
The government started to encourage the growth of drug manufacturing by Indian companies in the early 1960s, and with the Patents Act in 1970, enabled the industry to become what it is today. This patent act removed composition patents from food and drugs, and though it kept process patents, these were shortened to a period of five to seven years. The lack of patent protection made the Indian market undesirable to the multinational companies that had dominated the market, and while they streamed out, Indian companies started to take their places. They carved a niche in both the Indian and world markets with their expertise in reverse-engineering new processes for manufacturing drugs at low costs. Although some of the larger companies have taken baby steps towards drug innovation, the industry as a whole has been following this business model until the present.
MAJOR PLAYERS
RANBAXY LABORATORIES
(Ranbaxy Laboratories Limited is
Ranbaxy went public in 1973.)
(Public Profile)
Ranbaxy Laboratories Limited,
Earlier in June 2008, Ranbaxy entered into an alliance with one of the largest Japanese innovator companies, Daiichi Sankyo Company Ltd., to create an innovator and generic pharmaceutical powerhouse. The transformational deal will place Ranbaxy in a higher growth trajectory. The ranking of the combined entity will be catapulted to the No. 15th position in the global pharmaceutical space and it will emerge stronger in terms of its global reach and in its capabilities in drug development and manufacturing.
DR. REDDY'S LABORATORIES
(Dr. Reddy’s Laboratories Ltd. trading as Dr. Reddy's, founded in 1984 by Dr. K. Anji Reddy, has become
Dr. Reddy’s began as a supplier to Indian drug manufacturers, but it soon started exporting to other less-regulated markets – that had the advantage of not having to spend time and money on a manufacturing plant that that would gain approval from a drug licensing body such as the
By 2007, Dr. Reddy’s had six FDA-plants producing active pharmaceutical ingredients in India and seven FDA-inspected and ISO 9001 (quality) and ISO 14001 (environmental management) certified plants making patient-ready medications – five of them in India and two in the UK.
(Public Profile)
At Dr. Reddy's we aim at providing affordable and innovative medicines for healthier lives. We serve society’s important needs for affordable medicines through the API component of PSAI and the Global Generics business, and for innovative products that solve unmet medical needs through the CPS component of PSAI and the Proprietary Products Businesses.
Headquartered in
Our strong portfolio of businesses, geographies and products gives us an edge in an increasingly competitive global market and allows us to provide affordable medication to people across the world, regardless of geographic and socio-economic barriers.
NICHOLAS PIRAMAL
(Nicholas Piramal India Limited (Nicholas Piramal India Limited (NPIL) is India's second largest Pharmaceutical Healthcare company with a presence in the cardio-vascular segment, the antibiotics and respiratory segments, pain management, neuro-psychiatry and anti-diabetics segments and biotechnology.
NPIL came into existence in 1988 when it acquired Nicholas Laboratories from Sara Lee and in the last 15 years grown primarily on acquisitions, mergers and alliances. Some of NPIL's acquisitions include the Indian operations of Roche Products Ltd., Boehringer Mannheim India Ltd., Hoechst Marrion Roussel Ltd,'s Research Centre, Rhone Poulenc India Ltd., ICI India Ltd.'s Pharma Division and Aventis' Research facilities.
NPIL has joint ventures and alliances with F. Hoffmann-La Roche Ltd., Switzerland; Allergan Inc., USA; UK; Gilead Sciences, USA; Cheissi, Italy; and IVAX Corp; UK.)
(Public Profile)
Nicholas Piramal India Limited is one of
With growth fuelled through a strategy of partnerships, quality acquisitions, brand building, focused selling and manufacturing, NPIL's consolidated net sales turnover was US$ 313 million (INR 14.1 billion) in 2005-06 (April to March)".
CIPLA
(Cipla, Founded 1935, originally founded as The Chemical, Industrial & Pharmaceutical Laboratories is a prominent Indian pharmaceutical company, best-known outside its home country for producing low-cost anti-AIDS drugs for HIV-positive patients in developing countries. Cipla makes drugs to treat cardiovascular disease, arthritis, diabetes, weight control, depression and many other health conditions, and its products are distributed in more than 180 countries worldwide. Among the hundreds of generic medications it produces for international distribution are atorvastatin, amlodipine, fluoxetine, venlafaxine hydrochloride and metformin.)
(Public Profile)
Cipla is born
In 1935, he set up The Chemical, Industrial & Pharmaceutical Laboratories, which came to be popularly known as Cipla. He gave the company all his patent and proprietary formulas for several drugs and medicines, without charging any royalty. On August 17, 1935, Cipla was registered as a public limited company with an authorised capital of Rs 6 lakhs.
The search for suitable premises ended at 289,
Cipla was officially opened on September 22, 1937 when the first products were ready for the market. The Sunday Standard wrote: "The birth of Cipla which was launched into the world by Dr K A Hamied will be a red letter day in the annals of Bombay Industries. The first city in
BIOCON
(Biocon is
The company is headed by Kiran Mazumdar-Shaw. Biocon went for an IPO in 2004. Biocon became only the second Indian company to cross a market capitalization of one billion
(Public Profile)
Biocon’s fully integrated business model spans the entire drug value chain, from pre-clinical discovery to clinical development and through to commercialization. Our businesses in custom research (Syngene), clinical development (Clinigene) and biopharmaceuticals (Biocon) provide multiple revenue streams to balance risk, drive innovation, deliver products and accelerate growth. As we increase the complexity and scope of our own R&D and manufacturing operations, especially in new product discovery and development, we believe our custom and clinical research services will continue to offer important synergies.
Syngene : Pre-Clinical Discovery
Clinigene : Clinical Development
Biocon : Commercialisation
SERUM INSTITUTE OF
(Serum Institute of
(Public Profile)
Serum Institute of India Ltd. has established it's self as the world's largest producer of Measles and DTP group of vaccines. It is estimated that two out of every three children immunized in the world is vaccinated by a vaccine manufactured by Serum Institute. In fact, our range of products have been used in 140 countries across the globe.
Serum Institute of
INTAS BIOPHARMACEUTICALS
(Intas Biopharmaceuticals Ltd. is an Indian biotechnology company headquartered in Ahmedabad,
As an independent biopharmaceutical company of the Intas Group, the company has fully integrated biopharmaceutical operations with R&D facility and an EU-GMP certified bio-pharmaceutical manufacturing facility.
Intas Biopharma is also actively pursuing the Contract Research and Manufacturing Services (CRAMS) line of business. To expand its CRAMS business, Intas Biopharmaceuticals Ltd., in June 2008, acquired a
(Public Profile)
Intas Biopharmaceuticals Limited (IBPL) is a fully integrated biopharmaceutical company based out of Ahmedabad,
Intas Biopharmaceuticals is
Intas Biopharma has carved a niche in the biopharmaceutical arena for its world class Quality Standards, with the facility complying strictly with International Good Manufacturing Practices and guidelines laid down by the World Health Organization (WHO).
Products are under registration in more than 78 countries. Locally, the company has strategic tie-ups to penetrate the highly competitive Indian market. Intas Biopharma has entered into several supply and marketing agreements with reputed international companies in regulated and semi-regulated markets of Europe, Asia-Pacific,
BHARAT SERUMS
(Since inception in 1971, BSV has worked ceaselessly to research, develop, manufacture and market specialized biological, pharmaceutical and biotechnology products.
Today, BSV is one of the fast growing Indian bio-pharmaceutical companies. The product portfolio comprises of a wide range of products such as plasma derivatives, monoclonals, hormones, equine antitoxins and serums, antifungals, anaesthetics, cardiovascular and diagnostic products.
BSV is managed by an experianced Board of Directors, who are assisted by a team of dedicated and qualified professionals drawn from various disciplines. The management team comprises of qualified doctors, professionals and postgraduates having rich experience and expertise in their respective fields. )
(Public Profile)
Bharat Serums And Vaccines Limited (BSV) was incorporated to pursue an ambitious goal of introducing specialized healthcare products to meet the needs of a quality conscious market.
The Company manufactures and markets biological, pharmaceutical and biotechnology products. Today, BSV holds a formidable market share in
BSV has also sharpened its focus on R&D by continuous allocation of resources and manpower. The Company is introducing niche life saving injectibles, substantially improving the safety and efficacy of existing therapy.
LUPIN LABORATORIES
(Public Profile)
Lupin Limited, headquartered in
The Company has gained recognition as the world’s largest manufacturer of Tuberculosis drugs. Over the years, the Company has moved up the value chain and has not only mastered the business of certain intermediates and APIs, but has also leveraged its strengths to build a formidable formulations business. It has a significant presence in Cephalosporins, Cardiovasculars (prils and statins), Diabetology, Asthama and NSAIDs therapy segments.
During 2007, Lupin fast tracked its growth trajectory through two acquisitions. While the acquisition of Kyowa positioned the Company amongst the top ten generic pharma Companies in
ORCHID PHARMACEUTICALS
(Public Profile)
first year of operations (1994-95)
Orchid Chemicals & Pharmaceuticals Ltd (Orchid) was established in 1992 as a 100% Export Oriented Unit (EOU). Commencing operations in 1994, Orchid has achieved amazing and consistent growth, quantitatively and qualitatively to emerge among the Top-15 companies in the Indian pharmaceutical industry in a short span of fourteen years of operations.
Orchid has two manufacturing sites for APIs (at Alathur near Chennai and at
Orchid’s scientific and technical strengths have made it a partner of choice for several multinational corporations. Orchid has long-term exclusive marketing alliances with reputed global companies such as Apotex, Actavis, Dava and Hospira for distribution of Orchid’s products in the advanced markets of US and
PANACEA BIOTECH
(Public Profile)
1984 Panacea Drug (P) Ltd. was formed
Panacea Biotec is
The vaccines portfolio consists of oral polio vaccines (type I and type III), Enivac-HB (Hepatitis B vaccine), Enivac-HB Safsy, Ecovac-4 (DTwP+Hep B), Easyfour (DTwP+Hib), Easyfive (DTwP+Hep B+Hib). Vaccines in the offing are- Anthrax, Dengue, Japanese encephalitis and several others. Panacea Biotec has earned the distinction of being a WHO pre-qualified supplier of oral polio and Hepatitis-B vaccines and are in the process of obtaining similar pre-qualifications for other vaccines. Panacea Biotec is contributing in disease prevention and reducing the child mortality.
SUN PHARMACEUTICALS
(Established in 1983, Sun Pharma was a start-up company with five products. Since 1996, Sun has grown largely through a combination of internal growth, and acquisition of other pharmaceutical companies. For example, it bought US-based Caraco Pharm Labs, and ICN
Sun Pharmaceutical (or Sun Pharmaceutical Industries Limited) is an international pharmaceutical company based in
(Public Profile)
Sun Pharma came into existence as a startup with just 5 products in 1983. We are now an international speciality pharma company with over 7000 people, 17 manufacturing locations (including three in the
TORRENT PHARMACEUTICALS
(Torrent Pharmaceuticals Ltd. Founded 1959, is the flagship company of the Torrent Group. Based in Ahmedabad, it was promoted by U. N. Mehta initially as Trinity Laboratories Ltd. and was later renamed to its current name Torrent Pharmaceuticals Ltd.
Torrent Pharmaceuticals operates in more than 50 countries with over 1000 product registrations globally. Moreover, it has 5 fully owned subsidiares:
Torrent do Brasila in
Torrent Pharma Gmbh in
Torrent Pharma Ltd. in the
Zao Torrent in
Torrent Pharma Inc. in
Torrent Pharmaceuticals acquired Heumann Gmbh, a Pfizer group company in 2005.)
(Public Profile)
Enterprising individual, Shri. U
The foundations for Torrent were laid when 'Trinity Laboratories' began operations under the able guidance of Shri Mehta whose efforts are worthy of emulation.
'Trinity' was renamed 'Torrent' and with this not only did the company get a new name, it also focused on establishing its own manufacturing facilities in the early 80s. Torrent augmented its efforts with the expansion of its manufacturing capacity, emphasis on marketing and creating business opportunities through focus on exports. Torrent Pharmaceuticals Limited recorded a quantum leap in the year 1994. It has also been rated
WOCKHARDT
(Public Profile)
Mr. Habil Khorakiwala, the Chairman of Wockhardt Limited, founded the company in the early 1960s
Wockhardt today, is distinguished by a strong and growing presence in the world’s leading markets, with more than 65% of its revenue coming from Europe and the
The Company has its headquarters in
14 manufacturing plants in
Subsidiaries in US,
Marketing offices in Africa,
Wockhardt has a strong track record in acquisition management, with five successful acquisitions in the European market. These acquisitions have strengthened Wockhardt’s position in the high-potential markets of
Aiding Wockhardt's globalization plans are its fourteen world-class manufacturing plants in
CADILA HEALTHCARE
(Cadila Healthcare Founded 1954, is an Indian pharmaceutical company headquartered at Ahmedabad in Gujarat state of western
Cadila Laboratories was founded in 1952 by Shri Ramanbhai Patel (1925-2001), formerly a lecturer in the
In 1995 the Patel and Modi families split, with the Modi family's share being moved into a new company called Cadila Pharmaceuticals Ltd. and Cadila Healthcare became the Patel family's holding company. Cadila Healthcare did its IPO on the
In 2001 the company acquired another Indian pharmaceutical company called German Remedies. On June 25, 2007, the company signed an agreement to acquire 100 per cent stake in
(Public Profile)
From nine pharmaceutical production operations in India as well as a major R&D operation Zydus Cadila develops and manufactures a large range of pharmaceuticals as well as diagnostics, herbal products, skin care products and other OTC products. The company also makes Sugar Free,
Very few know this but still, pharma industry over the years has not only grown but has taken itself to greater heights of drug discovery and health care products. Up coming industry has played a major roll in Indian economy and also is been recognized by the government, for the same new revisions and policy makers has not only rewarded with special economic zone, tax free zone, and new module of research and development sector, but also has given equal importance to the small and medium scale industry to flourish together.
Article By:
Piyush Tripathi
Cell: +91-9824663306
Introducing Digital PPE Matrix 2.0 – Now Voice-Activated!
๐ Introducing Digital PPE Matrix 2.0 – Now Voice-Activated! ๐ค #InnovationInSafety #PPEMatrix #HSE A question came to us: ...
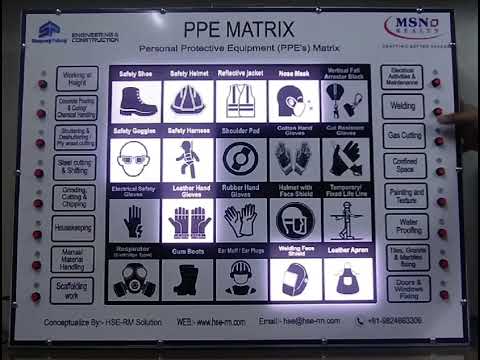
-
Chemical Safety Consciousness Sessions Chemical Safety by HSE-RM Solutions, we design customized training programs, evaluation base cert...
-
14-11-2023 Post Today Process Safety Implementation we must focuse specifically on inventory management, here are the key points to consider...
-
https://youtu.be/xydeGiZdckI Greetings, Identifying & Reporting 30th video of the series, effective recognition, Recognitio...