The art of the drug compounder Pharmacopoeia, is a book containing directions for the identification of samples and the preparation of compound medicines, and published by the authority of a government or a medical or pharmaceutical society.
HISTORY
• Arabic Book of Simple Drugs from Dioscorides’ De Materia Medica. Cumin & dill. c. 1334 By Kathleen Cohen in London's British Museum.
• Dioscorides, De Materia Medica, Byzantium, 15th century.
• Dioscorides De Materia Medica in Arabic, Spain, 12th-13th century.
Pharmacopoeia is considered to be the cradle of pharmacotherapy. Pedanius Dioscorides is famous for writing a five volume book in his native Greek (De Materia Medica - in the Latin translation) that is a precursor to all modern pharmacopoeias, and is one of the most influential herbal books in history. In fact it remained in use until about CE 1600.
Pharmacopoeia books were written by Persian physicians. These included The Canon of Medicine of Avicenna in 1025, and other pharmacopoeia books by Abu-Rayhan Biruni in the 11th century, Ibn Zuhr (Avenzoar) in the 12th century (and printed in 1491), and Ibn Baytar in the 14th century.
The term pharmacopoeia first appears as a distinct title in a work published at Basel in 1561 by Dr A. Foes, but does not appear to have come into general use until the beginning of the 17th century.
Over the years and century many revision and consideration from authorities, and regulatory act changed comities were formed. Finally, the first Edinburgh Pharmacopoeia was published in 1699 and the last in 1841; the first Dublin Pharmacopoeia in 1807 and the last in 1850.
The preparations contained in these three pharmacopoeias were not all uniform in strength, a source of much inconvenience and danger to the public, when powerful preparations such as dilute hydrocyanic acid were ordered in the one country and dispensed according to the national pharmacopoeia in another. As a result, the Medical Act of 1858 ordained that the General Medical Council should publish a book containing a list of medicines and compounds, to be called the British Pharmacopoeia, which would be a substitute throughout Great Britain and Ireland for the separate pharmacopoeias. Hitherto these had been published in Latin. The first British Pharmacopoeia was published in the English language in 1864, but gave such general dissatisfaction both to the medical profession and to chemists and druggists that the General Medical Council brought out a new and amended edition in 1867. This dissatisfaction was probably owing partly to the fact that the majority of the compilers of the work were not engaged in the practice of pharmacy, and therefore competent rather to decide upon the kind of preparations required than upon the method of their manufacture. The necessity for this element in the construction of a pharmacopoeia is now fully recognized in other countries, in most of which pharmaceutical chemists are represented on the committee for the preparation of the legally recognized manuals.
There are national and international pharmacopoeias, like the EU and the US pharmacopoeias. All the pharmacopoeias were issued under the authority of government, and their instructions have the force of law in their respective territories, except that of the United States, which was prepared by commissioners appointed by medical and pharmaceutical societies, and has no other authority, although generally accepted as the national textbook.
Increased facilities for travel have brought into greater prominence the importance of an approach to uniformity in the formulae of the more powerful remedies, in order to avoid danger to patients when a prescription is dispensed in a different country from that in which it was written. Nonetheless, some progress has been made under the banner of the ICH (The International Conference on Harmonisation of Technical Requirements for Registration of Pharmaceuticals for Human Use:www.ich.org), a tri-regional organisation that represents the drug regulatory authorities of the European Union, Japan and the United States. Representatives from the Pharmacopoeias of these three regions have met twice yearly since 1990 in the Pharmacopoeial Discussion Group to try to work towards "compendial harmonisation"’. Specific monographs are proposed, and if accepted, proceed through stages of review and consultation leading to adoption of a common monograph that provides a common set of tests and specifications for a specific material.
The rapid increase in medical and pharmaceutical knowledge renders necessary frequent new editions of the national pharmacopoeias, the office of which is to furnish definite formulae for preparations that have already come into extensive use in medical practice, so as to ensure uniformity of strength, and to give the characters and tests by which their purity and potency may be determined. each new edition requires several years to carry out numerous experiments for devising suitable formulae, so that the current Pharmacopoeia can never be quite up to date. This difficulty has hitherto been met by the publication of such nonofficial formularies as Squire's Companion to the Pharmacopoeia and Martindale: The complete drug reference (formerly Martindale's : The Extra Pharmacopoeia), in which all new remedies and their preparations, uses and doses are recorded, and in the former the varying strengths of the same preparations in the different pharmacopoeias are also compared (Squire's was incorporated into Martindal in 1952). The need of such works to supplement the Pharmacopoeia is shown by the fact that they are even more largely used than the Pharmacopoeia itself, the first issued in 18 editions and the second in 13 editions at comparatively short intervals. In the UK, the task of elaborating a new Pharmacopoeia is entrusted to a body of a purely medical character, and legally the pharmacist has not, contrary to the practice in other countries, a voice in the matter, notwithstanding the fact that, although the medical practitioner is naturally the best judge of the drug or preparations that will afford the best therapeutic result, he is not so competent as the pharmacist to say how that preparation can be produced in the most effective and satisfactory manner, nor how the purity of drugs can be tested.
Some difficulty has arisen since the passing of the Adulteration of Food and Drugs Act[citation needed] concerning the use of the Pharmacopoeia as a legal standard for the drugs and preparations contained in it. The Pharmacopoeia is defined in the preface as only "intended to afford to the members of the medical profession and those engaged in the preparation of medicines throughout the British Empire one uniform standard and guide whereby the nature and composition of, substances to be used in medicine may be ascertained and determined." It is obvious that it cannot be an encyclopaedia of substances used in medicine, and can only be used as a standard for the substances and preparations contained in it, and for no others. It has been held in the Divisional Courts (Dickins v. Randerson) that the Pharmacopoeia is a standard for official preparations asked for under their pharmacopoeial name. But there are many substances in the Pharmacopoeia which are not only employed in medicine, but have other uses, such as sulphur, gum benzoin, tragacanth, gum arabic, ammonium carbonate, beeswax, oil of turpentine, linseed oil, and for these a commercial standard of purity as distinct from a medicinal one is needed, since the preparations used in medicine should be of the highest possible degree of purity obtainable, and this standard would be too high and too expensive for ordinary purposes. The use of trade synonyms in the Pharmacopoeia, such as saltpetre for purified potassium nitrate, and milk of sulphur for precipitated sulphur, is partly answerable for this difficulty, and has proved to be a mistake, since it affords ground for legal prosecution if a chemist sells a drug of ordinary commercial purity for trade purposes, instead of the purified preparation which is official in the Pharmacopoeia for medicinal use. This would not be the case if the trade synonym were omitted. For many drugs and chemicals not in the Pharmacopoeia there is no standard of purity that can be used under the Adulteration of Food and Drugs Act, and for these, as well as for the commercial quality of those drugs and essential oils which are also in the Pharmacopoeia, a legal standard of commercial purity is much needed. This subject formed the basis of discussion at several meetings of the Pharmaceutical Society, and the results have been embodied in a work entitled Suggested Standards for Foods and Drugs, by C. G. Moor, which indicates the average degree of purity of many drugs and chemicals used in the arts, as well as the highest degree of purity obtainable in commerce of those used in medicine.
Another legal difficulty connected with modern pharmacopoeias is the inclusion in some of them of synthetic chemical remedies, the processes for preparing which have been patented, whilst the substances are sold under trade-mark names such as verona. The scientific chemical name is often long and unwieldy, and the physician prefers when writing a prescription to use the shorter name under which it is sold by the patentees. In this case the pharmacist is compelled to use the more expensive patented article and the patient complains of the price. If he uses the same article under its pharmacopoeial name when the patented article is prescribed s/he lays oneself open to prosecution by the patentee for infringement of patent rights. The only plan, therefore, is for the physician to use the chemical name (which cannot be patented) as given in the Pharmacopoeia, or for those synthetic remedies not included in the Pharmacopoeia, to use the scientific and chemical name given in the British Pharmaceutical Codex.
TRANSFORMATION
From new discoveries to developments, pharmacopoeia guides to technology, the interactions that occur between a living organism and exogenous chemicals that alter normal biochemical function. Substances with medicinal properties, are considered pharmaceuticals. The field encompasses drug composition and properties, interactions, toxicology, therapy, and medical applications and antipathogenic capabilities. A variety of topics involved with pharmacology, including neuropharmacology, renal pharmacology, human metabolism, intracellular metabolism, and intracellular regulation. Pharmacology is not synonymous with pharmacy, which is the name used for a profession, though in common usage the two terms are confused at times. Pharmacology deals with how drugs interact within biological systems to affect function. It is the study of drugs, of the body's reaction to drugs, the sources of drugs, their nature, and their properties. In contrast, pharmacy is a medical science concerned with the safe and effective use of medicines.
An origin of clinical pharmacology is in middle Ages in Avicenna's The Canon of Medicine, Peter of Spain's Commentary on Isaac, and John of St Amand's Commentary on the Antedotary of Nicholas. Pharmacology as a scientific discipline did not further advance until the mid-19th century amid the great biomedical resurgence of that period. Before the second half of the nineteenth century, the remarkable potency and specificity of the actions of drugs such as morphine, quinine and digitalis were explained vaguely and with reference to extraordinary chemical powers and affinities to certain organs or tissues. The first pharmacology department was set up by Buchheim in 1847, in recognition of the need to understand how therapeutic drugs and poisons produced their effects.
In the United States, the Food and Drug Administration (FDA) is responsible for creating guidelines for the approval and use of drugs. The FDA requires that all approved drugs fulfill two requirements:
1. The drug must be found to be effective against the disease for which it is seeking approval.
2. The drug must meet safety criteria by being subject to extensive animal and controlled human testing.
Gaining FDA approval usually takes several years to attain. Testing done on animals must be extensive and must include several species to help in the evaluation of both the effectiveness and toxicity of the drug. The dosage of any drug approved for use is intended to fall within a range in which the drug produces a therapeutic effect or desired outcome.
The safety and effectiveness of prescription drugs in the U.S. is regulated by the federal Prescription Drug Marketing Act of 1987.
The Medicines and Healthcare products Regulatory Agency (MHRA) has a similar role in the UK.
Early pharmacologists focused on natural substances, mainly plant extracts. Pharmacology developed in the 19th century as a biomedical science that applied the principles of scientific experimentation to therapeutic contexts.
The genetic revolution has pushed to the forefront a concept that is at the very heart of pharmacology and therapeutics – the right drug for the right target in the right patient and delivered at the right dose. In some areas such as cancer treatments, examples of specific tumour mutations that dictate the response to drugs is a reality. This will influence the nature of future clinical trials. The bigger challenge lies in understanding whether the same will be true for common germline genetic variation (polymorphisms) in the general population. Will common genetic variation influence response to treatment? The complexity of turning this into a clinically meaningful risk score is such that attention has turned towards pharmaceuticals. Is drug failure due in individual patients due to genetic variation? Could drug safety be improved by taking into account individual genetic risk? Data on genetic variation influencing efficacy are sparse.
On another level, by taking reductionism and integrated approaches, genetics and molecular pharmacology are beginning to unravel the enigmatic problem of drug receptor heterogeneity. The future promises new generations of drugs that could selectively target one subtype in a family of similar proteins to the therapeutic advantage of the patient while limiting commonly accepted and often debilitating side effects.
Pharmacology as a chemical science is practiced by pharmacologists. Viz.:
• Clinical pharmacology - the medical field of medication effects on humans
Clinical pharmacology connects the gap between medical practice and laboratory science. The main objective is to promote the safety of prescription, maximize the drug effects and minimize the side effects. It is important that there be association with pharmacists skilled in areas of drug information, medication safety and other aspects of pharmacy practice related to clinical pharmacology.
Clinical pharmacologists have a rigorous medical and scientific training which enables them to evaluate evidence and produce new data through well designed studies. Clinical pharmacologists have access to enough outpatients for clinical care, teaching and education, and research as well be supervised by medical specialists. Their responsibilities to patients include, but are not limited to analyzing adverse drug effects, therapeutics, and toxicology including reproductive toxicology, cardiovascular risks, perioperative drug management and psychopharmacology.
• Neuro- and psychopharmacology (effects of medication on behavior and nervous system functioning),
Neuro is a study a wide range of substances with various types of psychoactive properties. The professional and commercial fields of pharmacology and psychopharmacology do not mainly focus on psychedelic or recreational drugs, as the majority of studies are conducted for the development, study, and use of drugs for the modification of behavior and the alleviation of symptoms, particularly in the treatment of mental disorders (psychiatric medication). While studies are conducted on all psychoactives by both fields, psychopharmacology focuses primarily on the psychoactive and chemical interactions with the brain.
Psychoactive drugs may originate from natural sources such as plants and animals, or from artificial sources such as chemical synthesis in the laboratory. These drugs interact with particular target sites or receptors found in the nervous system to induce widespread changes in physiological or psychological functions.
• Pharmacogenetics (clinical testing of genetic variation that gives rise to differing response to drugs)
The terms pharmacogenomics and pharmacogenetics tend to be used interchangeably, and a precise, consensus definition of either remains elusive. Pharmacogenetics is generally regarded as the study or clinical testing of genetic variation that gives rise to differing response to drugs, while pharmacogenomics is the broader application of genomic technologies to new drug discovery and further characterization of older drugs.
• Pharmacogenomics (application of genomic technologies to new drug discovery and further characterization of older drugs)
Pharmacogenomics is the branch of pharmacology which deals with the influence of genetic variation on drug response in patients by correlating gene expression or single-nucleotide polymorphisms with a drug's efficacy or toxicity. By doing so, pharmacogenomics aims to develop rational means to optimise drug therapy, with respect to the patients' genotype, to ensure maximum efficacy with minimal adverse effects. Such approaches are advent of "personalized medicine"; in which drugs and drug combinations are optimized for each individual's unique genetic makeup.
Pharmacogenomics is the whole genome application of pharmacogenetics, which examines the single gene interactions with drugs.
• Pharmacoepidemiology (study of effects of drugs in large numbers of people)
Pharmacoepidemiology borrows from both pharmacology and epidemiology. Thus, pharmacoepidemiology can be called a bridge science spanning both pharmacology and epidemiology. Pharmacology is the study of the effect of drugs and clinical pharmacology is the study of effect of drugs in humans. Part of the task of clinical pharmacology is to provide a risk benefit assessment for the effect of drugs in patients. Doing the studies needed to provide an estimate of the probability of beneficial effects in populations, or the probability of adverse effects in populations and other parameters relating to drug use may benefit from using epidemiological methodology. Pharmacoepidemiology then can also be defined as the application of epidemiological methods to pharmacological issues.
Pharmacoepidemiology benefits from the methodology developed in general epidemiology and may further develop them for applications of such methodology unique to pharmacoepidemiology. There are also some areas that are altogether unique to pharmacoepidemiology, e.g., pharmacovigilance. Pharmacovigilance is a type of continual monitoring for unwanted effects and other safety-related aspects of drugs that are already on the market. In practice, pharmacovigilance refers almost exclusively to the spontaneous reporting systems which allow health care professionals and others to report adverse drug reactions to a central agency. The central agency can then combine reports from many sources to produce a more informative safety profile for the drug product than could be done based on one or a few reports from one or a few health care professionals.
• Toxicology study of harmful effects of drugs
Study of the adverse effects of chemicals on living organisms. It is the study of symptoms, mechanisms, treatments and detection of poisoning, especially the poisoning of people.
Theoretical pharmacology
Posology - how medicines are dosed
Pharmacognosy a branch of pharmacology dealing especially with the composition, use, and development of medicinal substances of biological origin and especially medicinal substances obtained from plants also known as deriving medicines from plants
PHARMA MACHINERY & EQUIPMENTS: BY PIYUSH TRIPATHI
MANUFACTURING
Manufacturing is the use of machines, tools and labor to make things for use or sale. The term may refer to a range of human activity, from handicraft to high tech, but is most commonly applied to industrial production, in which raw materials are transformed into finished goods on a large scale. Such finished goods may be used for manufacturing other, more complex products, such as household appliances or automobiles, or sold to wholesalers, who in turn sell them to retailers, who then sell them to end users - the "consumers".
Manufacturing takes place under all types of economic systems. In a free market economy, manufacturing is usually directed toward the mass production of products for sale to consumers at a profit. In a collectivist economy, manufacturing is more frequently directed by the state to supply a centrally planned economy. In free market economies, manufacturing occurs under some degree of government regulation.
Modern manufacturing includes all intermediate processes required for the production and integration of a product's components. Some industries, such as semiconductor and steel manufacturers use the term fabrication instead. The manufacturing sector is closely connected with engineering and industrial design. Pharmaceutical machinery manufactures have understood the concept behind the process involvement for development of drug, machinery are developed as per client process requirement. Need for such development required in-depth study and monitoring process requirements of clients. Machinery manufactures updated their facilities by latest automated machinery for manufacturing parts, in addition to this there are also other visible trends that can explain committed interest of Indian machinery manufacturers further:
- Manufactures are going for CNC machine to get quality output
- Use of efficient and modern gadgets in the machine, like, VFD, PLC etc.
- Quality approvals and Trademarks, getting ISO approval and international certificate approval for quality manufacturing are also a part of dedication.
- To adapt and implement prototype machines are imported by manufactures.
- Tie-up & Collaboration for technology transfer with international manufactures.
- Expanding high tech facility to meet rising global demand.
Indian Pharma Machinery Manufacturers Association (IPMMA) is also established to work as entrepreneur’s team and also sets technological fairs and international and domestic meet providing a platform for B to B meets and bringing client and manufacture directly in touch with each other and working for mutual benefit.
PHARMACEUTICAL MACHINERY SEGMENT
Industrial segment specially pharmaceutical process and packaging sector have adopted modern means of process evolvement, manufactures have upgraded and adapted modern means of process plant development for providing controlled economical and efficient setups to cope up with the up coming trend and technological advancements. In many production plants, pharmaceutical manufacturers have developed a high degree of automation. Milling and micronizing machines, which pulverize substances into extremely fine particles, are used to reduce bulk chemicals to the required size. These finished chemicals are combined and processed further in mixing machines. The mixed ingredients may then be mechanically capsulated, pressed into tablets, or made into solutions. One type of machine, for example, automatically fills, seals, and stamps capsules. Other machines fill bottles with capsules, tablets, or liquids, and seal, label, and package the bottles.
At the time of industrialization growth flow in 60’s and 70’s the pharmaceutical industry big or small were forced to imported machines from Europe for their processing and packaging needs. During the phase entrepreneurs, engineers in India realized the need for development in the sector for better improvement and meeting requirements of the fastest growing Industry Pharmaceutical process and packing. After the declaration of industrial policies in the mid 70's Indian government introduced very high import duties and restrictive import licensing policies. This resulted in a spark in the Indian engineers to prove their excellence as enterprises to manufacture machines locally. Engineers had the skills and now the support of industry and associations were form to cater the domestic market for better improvement as perhaps the only route for the pharmaceutical industry to enhance production and cater to the growing demands of the domestic market.
With this big a size of the industry a proper setup development plan and skill to cater the need was inevitable. Pharmaceutical Industry grew at the most fastest rate in India for its mineral rich resources, ore availability, raw material power house of such basic ingredients which were cheaply available in local market strengthen the growth. To support the industry Pharmaceutical Machinery Manufactures also upgraded themselves and adapted to a marketing plan. To ensure proper flow and meeting technological upgrades manufactures had to plan a proper strategy for not only meeting requirements but also giving technological upgrade the equipments for faster and efficient working.
DOMESTIC MANUFACTURING CHALLENGES
The machinery manufacturing industry, like all international manufacturers, continues to evolve. Domestic and foreign competition has required the industry to adopt new technologies and techniques to lower costs and raise the productivity of its workforce. For example, using high-technology production techniques, including robots, computers, and programmable equipment results in productivity gains and helps to maximize the use of available equipment and workers. Increasing technology and automation also reduces the number of unskilled workers needed in the production process.
Pressures to reduce costs and maximize profits have also caused manufacturers in the industry to adopt new business practices. One example is the practice of contracting out support functions, such as janitorial and security jobs, and increasingly some administrative services and warehouse and shipping jobs. Rather than employ workers directly for these jobs, a manufacturer will often contract with another company that specializes in providing these services. This practice reduces costs by forcing service providers to compete for the work, allows manufacturers to focus on their core design and production activities, and increases manufacturers’ flexibility by letting them add and subtract contract workers more easily than they could hire and fire employees.
These changes have had a profound effect on the machinery manufacturing workforce. By automating many of the production processes and outsourcing many of the administrative and support functions, it has reduced the need for many less skilled workers and increased the skill level required for the remaining workers. These changes are allowing the industry to remain competitive and meet the demand for machinery that other industries rely on.
One of the greater challenge faced is specialization in restricted field of work to set up a work force which requires, Engineers specialize in a particular facet of design. Mechanical engineers design the moving parts of the machine, such as the gears, levers, and pistons in engine and hydraulic systems. They also direct the work of mechanical engineering technicians, who run tests on materials and parts before they are assembled into the final product. For machines with complicated electric or electronic systems, electrical and electronics engineers also assist in the design and testing process. Industrial engineers determine how best to allocate the resources of the factory—both workers and equipment—for optimal production. Once a design is finished and simulation testing complete, mechanical drafters creates the plans that production workers use in the assembly of the machine. They provide specifications and diagrams for each part required, as well as assembly instructions for the final product. Computer control programmers and operators manage the automatic metalworking machines that can mass produce individual parts. They also write programs based upon the specifications of the part that defines what operation the machine should perform. Machinists produce precision parts that require particular skill or that are needed in quantities too small to require the use of automated machinery. Welding, soldering, and brazing workers operate machines that join two or more pieces of metal together; they may also weld manually as well.
Once all of the parts have been made, it is the responsibility of assemblers and fabricators to put them all together to finish the product. Some assemblers specialize in one particular stage of the process, while others, such as team assemblers, work as a group and may contribute to an entire subassembly process. While there has been increased automation of the assembly process, many parts of the products still have to be put together and fastened by hand. When assembly is complete, painting workers apply paint or a protective coating to the exterior of the machine.
While quality control is a responsibility of all production workers, it is the primary focus of inspectors, testers, samplers, and weighers. These workers monitor the entire production stage, making sure that individual parts, as well as the finished product, meet the standards set by the company.
In addition to production-specific occupations, this industry has various managers and administrative support personnel to handle functions such as human relations, accounting, and general management. The sales function for many companies is increasingly important. Sales representatives and sales engineers often work together to market the company’s machines to potential buyers, demonstrating how the machine may reduce costs or increase sales. They also explain how to operate the machine and answer buyer’s questions. Sales engineers in particular use their technical background to advise clients on how the machine can best be applied in their individual circumstances and to suggest custom designs or modifications to the equipment as needed.
MANAGEMENT ASPECT OF MANUFACTURING
The main factor affecting the level of employment in the machinery manufacturing industry is the high rate of productivity growth. Increases in productivity allow companies to produce more goods with the same number of workers. Even though output in machinery manufacturing is expected to increase significantly, firms are capable to meet the increase through higher productivity of existing workers, rather than by creating new jobs and increasing work force.
A second factor expected to cause some employment declines in machinery manufacturing is the growing number of imported parts. Earlier only raw material was available now finish part machined and finished are also available and raw material suppliers are supplying the same to compete with the competition. This industry is less likely to lose a large part of its output to imports from other countries than some other manufacturing industries. The large size and complexity of many of the types of machinery made by this industry and the relatively skilled workforce it requires is an advantage that many manufacturing industries do not share.
The manufacturing focus in the early-to-mid-2000s was on new and diverse products to meet the individual needs and desires of the market. Companies in 2003 wanted "quick changeover capabilities, flexibility, and fast speeds" more than any other features. Consequently, the industry was expecting continued growth to meet demands for newer and better packaging machinery, replacing older equipment with newer, faster, more efficient, and more automated machines. Trends toward lightweight, individually designed, flexible, and reusable packaging increased demand for the design of machines that could manufacture such packaging.
Demand for machinery is expected to remain strong. Machinery is important for all industries because it boosts their productivity, and advances in technology will make machinery even more efficient and thus more desirable. Demand for machinery is highly sensitive to cyclical swings in the economy, however, causing employment in machinery manufacturing to fluctuate. During periods of economic prosperity, companies invest in new equipment, such as machinery, in order to boost production. When economic growth slows, however, many companies are reluctant to purchase new machinery. These changes in demand cause machinery manufacturers to replace fewer workers who leave or even lay off some workers.
Although overall employment in the machinery manufacturing industry is expected to decline, the outlook for occupations will vary; some will experience larger declines than others, while some will even experience growth instead. Increased automation and more efficient production processes will cause employment declines in assembler and fabricator occupations. Office and administrative support workers will also experience declines as a result of increased automation and contracting out. Employment in professional and management occupations will experience smaller declines relative to other occupations in the industry; engineers in particular will experience very good employment opportunities, as they are responsible for increasing innovation and competitiveness in the industry.
USE OF PROCESS & PACKAGING MACHINERY
Primary use of process and packaging machinery is to elated equipment and it's uses.
BLENDING & MIXING
Blending is to combine or mix so that the constituent parts are indistinguishable from one another and to obtain a mixture of particular character, quality or consistency. Blending machines such as Agitators, Conical blenders, Continuous mixers, Dough mixers, Emulsifiers, Gas, Homogenizers, In line mixers, Meat mixers, Paste mixers, Plough blade, Powder mixers, Ribbon mixers, Solid phase mixers, Viscous product mixers, Z Blade mixers.
GRANULATORS
Current good manufacturing practices increasingly require that product is fully contained during processing to protect operators and environment. Integrated process systems not only offer containment but improved productivity through automation, increased yield and efficient cleaning procedures. The granulation process can be one of the following; Low shear dry granulation, high shear wet granulation and melt granulating. Mixing and granulating can be combined into one machine.
HOMOGENIZERS
Homogenizer is to reduce to particles and disperse throughout a fluid. Inline homogenizers are the ideal solution for continuous processing of emulsions and dispersions.
MILLING & SIEVING
The integration of all types of mills and sieves can be tailored to suit the individual needs. There can be specific applications such as hoist mounted systems and high powder containment levels. Other design options include nitrogen purge systems and CIP systems. Quick change over between products is essential and the application of integrated control systems is needed. There are various types of mills such as toothed colloid, corundum stone and perforated disc mills. Product is loaded via a hopper that can also be fitted with a feed screw, or via a pump. The milling zone is sealed by a single or double-acting mechanical seal, with no dead space. All product contact surfaces should be very easily cleaned with no need for dismantling (CIP). Thorough washing of all static seals during the cleaning process complies with the hygiene standards. In all industrial sectors, demands in terms of flexibility and hygiene management are constantly on the increase.
POWDER HANDLING
Common problems include material blockages where sticky poor flowing materials will not discharge from an IBC. Segregation of blended material is another common problem. Segregation can be caused during the discharge from the IBC. It can also occur after discharge from the IBC when product is allowed to fall through long chutes in free fall, and displaced air from below is forced back up the chute and separates the finer particles from the coarser particles.
PROCESS VESSELS
Processing vessels need to be of a high quality construction and are widely used by the food and processing industries. A selection of sizes, specifications and agitator combinations are available to suit most needs. Stainless steel is used for all fabricated parts to meet industry requirements. Pressurized jackets for heating by steam or water facilitate boiling, cooking, melting, dispersion and mixing of products. Vessels can also be equipped for oil heating or water cooling.
IBC / INDUSTRIAL BULK CONTAINER
Container blending has long been established as the most efficient method of blending granules and powders in the pharmaceutical manufacturing process. Reduced loading and unloading times, reduced cleaning time of both machinery and room, improved containment and batch integrity have established IBC blending as the pharmaceutical industry’s technology of choice.
PROCESS PUMPS
Various types of process pumps can be used depending upon the type of product to be moved between or within the complete process line of the various integrated sub systems. Pumps such as centrifugal, diaphragm, dosing, gear, metering, reciprocation and vacuum can be used. For example, vacuum pumps will be used for powder handling but screw metering drives can be used for more accurate powder movement.
PROCESS CLEANING MACHINES
The cleaning of the process machines will be mainly carried out by CIP (Clean In Place) systems. Depending on the sensitivity of the product being produced, the equipment may be cleaned aseptically and therefore eliminating any possible contamination from outside.
STERILIZING MACHINES
Sterilizing machines can also be called, Autoclaves and Retorts. There three main types of sterilizing system; static, rotary and pilot or laboratory systems.
GENERAL CHARACTERISTICS ARE:-
• Steam-Water sprays mix.
• Top shower for cans and glass jars plus side shower for pouches and trays
• Indirect cooling system by heat exchanger allows water recovery.
• All vessel, pipe work and valves and heat exchanger in stainless steel materials
• Insulated shell with mirror polished stainless steel cladding
• PLC control with modem connection allows remote troubleshooting and servicing
• Process monitoring in the operator interface with complete information of temperature, pressure, time and flow
• Easy product recipe setup with password protected access
• Optimum heat distribution (+/-0,5 ยบC)
• Accurate pressure control (+/- 0,05 bar)
The rotary machines will use inverter drives for accurate control during the sterilizing process. There is also associated equipment such as basket trolleys and automatic loading systems available to fully automate the sterilizing process of product.
PROCESS CONTROL SYSTEMS
Compliance, traceability, consistency, and reliability of measurement data are primary concerns for the pharmaceutical industry. The control system is needed to verify the product quality through measuring, counting, inspection and testing of the manufacturing process. Operator input data; scanning systems and feedback systems are used.
PROCESS AND PACKAGING MACHINERY IN GENERAL
These machine types are very general indeed. Each area or sector of packaging equipment can be expanded upon to reveal the various applications that are available today. As technology advances, packaging machines are becoming more and more advanced to not only meet the current demands but to try and "future proof" the packaging equipment and product development within an organization. This can have a bearing on machine costs plus the interchangeability of operators and training. Packaging machines can be integrated into an existing line to enhance the production output or to reduce the labor and down type to pack the product. From single machine, to small systems or complete lines containing more than one new or existing / reconditioned packaging machine can be installed. Depending on the size of the installation, project process line and packaging machinery are available domestically to withstand & compete with market requirements.
Manufacturing is the use of machines, tools and labor to make things for use or sale. The term may refer to a range of human activity, from handicraft to high tech, but is most commonly applied to industrial production, in which raw materials are transformed into finished goods on a large scale. Such finished goods may be used for manufacturing other, more complex products, such as household appliances or automobiles, or sold to wholesalers, who in turn sell them to retailers, who then sell them to end users - the "consumers".
Manufacturing takes place under all types of economic systems. In a free market economy, manufacturing is usually directed toward the mass production of products for sale to consumers at a profit. In a collectivist economy, manufacturing is more frequently directed by the state to supply a centrally planned economy. In free market economies, manufacturing occurs under some degree of government regulation.
Modern manufacturing includes all intermediate processes required for the production and integration of a product's components. Some industries, such as semiconductor and steel manufacturers use the term fabrication instead. The manufacturing sector is closely connected with engineering and industrial design. Pharmaceutical machinery manufactures have understood the concept behind the process involvement for development of drug, machinery are developed as per client process requirement. Need for such development required in-depth study and monitoring process requirements of clients. Machinery manufactures updated their facilities by latest automated machinery for manufacturing parts, in addition to this there are also other visible trends that can explain committed interest of Indian machinery manufacturers further:
- Manufactures are going for CNC machine to get quality output
- Use of efficient and modern gadgets in the machine, like, VFD, PLC etc.
- Quality approvals and Trademarks, getting ISO approval and international certificate approval for quality manufacturing are also a part of dedication.
- To adapt and implement prototype machines are imported by manufactures.
- Tie-up & Collaboration for technology transfer with international manufactures.
- Expanding high tech facility to meet rising global demand.
Indian Pharma Machinery Manufacturers Association (IPMMA) is also established to work as entrepreneur’s team and also sets technological fairs and international and domestic meet providing a platform for B to B meets and bringing client and manufacture directly in touch with each other and working for mutual benefit.
PHARMACEUTICAL MACHINERY SEGMENT
Industrial segment specially pharmaceutical process and packaging sector have adopted modern means of process evolvement, manufactures have upgraded and adapted modern means of process plant development for providing controlled economical and efficient setups to cope up with the up coming trend and technological advancements. In many production plants, pharmaceutical manufacturers have developed a high degree of automation. Milling and micronizing machines, which pulverize substances into extremely fine particles, are used to reduce bulk chemicals to the required size. These finished chemicals are combined and processed further in mixing machines. The mixed ingredients may then be mechanically capsulated, pressed into tablets, or made into solutions. One type of machine, for example, automatically fills, seals, and stamps capsules. Other machines fill bottles with capsules, tablets, or liquids, and seal, label, and package the bottles.
At the time of industrialization growth flow in 60’s and 70’s the pharmaceutical industry big or small were forced to imported machines from Europe for their processing and packaging needs. During the phase entrepreneurs, engineers in India realized the need for development in the sector for better improvement and meeting requirements of the fastest growing Industry Pharmaceutical process and packing. After the declaration of industrial policies in the mid 70's Indian government introduced very high import duties and restrictive import licensing policies. This resulted in a spark in the Indian engineers to prove their excellence as enterprises to manufacture machines locally. Engineers had the skills and now the support of industry and associations were form to cater the domestic market for better improvement as perhaps the only route for the pharmaceutical industry to enhance production and cater to the growing demands of the domestic market.
With this big a size of the industry a proper setup development plan and skill to cater the need was inevitable. Pharmaceutical Industry grew at the most fastest rate in India for its mineral rich resources, ore availability, raw material power house of such basic ingredients which were cheaply available in local market strengthen the growth. To support the industry Pharmaceutical Machinery Manufactures also upgraded themselves and adapted to a marketing plan. To ensure proper flow and meeting technological upgrades manufactures had to plan a proper strategy for not only meeting requirements but also giving technological upgrade the equipments for faster and efficient working.
DOMESTIC MANUFACTURING CHALLENGES
The machinery manufacturing industry, like all international manufacturers, continues to evolve. Domestic and foreign competition has required the industry to adopt new technologies and techniques to lower costs and raise the productivity of its workforce. For example, using high-technology production techniques, including robots, computers, and programmable equipment results in productivity gains and helps to maximize the use of available equipment and workers. Increasing technology and automation also reduces the number of unskilled workers needed in the production process.
Pressures to reduce costs and maximize profits have also caused manufacturers in the industry to adopt new business practices. One example is the practice of contracting out support functions, such as janitorial and security jobs, and increasingly some administrative services and warehouse and shipping jobs. Rather than employ workers directly for these jobs, a manufacturer will often contract with another company that specializes in providing these services. This practice reduces costs by forcing service providers to compete for the work, allows manufacturers to focus on their core design and production activities, and increases manufacturers’ flexibility by letting them add and subtract contract workers more easily than they could hire and fire employees.
These changes have had a profound effect on the machinery manufacturing workforce. By automating many of the production processes and outsourcing many of the administrative and support functions, it has reduced the need for many less skilled workers and increased the skill level required for the remaining workers. These changes are allowing the industry to remain competitive and meet the demand for machinery that other industries rely on.
One of the greater challenge faced is specialization in restricted field of work to set up a work force which requires, Engineers specialize in a particular facet of design. Mechanical engineers design the moving parts of the machine, such as the gears, levers, and pistons in engine and hydraulic systems. They also direct the work of mechanical engineering technicians, who run tests on materials and parts before they are assembled into the final product. For machines with complicated electric or electronic systems, electrical and electronics engineers also assist in the design and testing process. Industrial engineers determine how best to allocate the resources of the factory—both workers and equipment—for optimal production. Once a design is finished and simulation testing complete, mechanical drafters creates the plans that production workers use in the assembly of the machine. They provide specifications and diagrams for each part required, as well as assembly instructions for the final product. Computer control programmers and operators manage the automatic metalworking machines that can mass produce individual parts. They also write programs based upon the specifications of the part that defines what operation the machine should perform. Machinists produce precision parts that require particular skill or that are needed in quantities too small to require the use of automated machinery. Welding, soldering, and brazing workers operate machines that join two or more pieces of metal together; they may also weld manually as well.
Once all of the parts have been made, it is the responsibility of assemblers and fabricators to put them all together to finish the product. Some assemblers specialize in one particular stage of the process, while others, such as team assemblers, work as a group and may contribute to an entire subassembly process. While there has been increased automation of the assembly process, many parts of the products still have to be put together and fastened by hand. When assembly is complete, painting workers apply paint or a protective coating to the exterior of the machine.
While quality control is a responsibility of all production workers, it is the primary focus of inspectors, testers, samplers, and weighers. These workers monitor the entire production stage, making sure that individual parts, as well as the finished product, meet the standards set by the company.
In addition to production-specific occupations, this industry has various managers and administrative support personnel to handle functions such as human relations, accounting, and general management. The sales function for many companies is increasingly important. Sales representatives and sales engineers often work together to market the company’s machines to potential buyers, demonstrating how the machine may reduce costs or increase sales. They also explain how to operate the machine and answer buyer’s questions. Sales engineers in particular use their technical background to advise clients on how the machine can best be applied in their individual circumstances and to suggest custom designs or modifications to the equipment as needed.
MANAGEMENT ASPECT OF MANUFACTURING
The main factor affecting the level of employment in the machinery manufacturing industry is the high rate of productivity growth. Increases in productivity allow companies to produce more goods with the same number of workers. Even though output in machinery manufacturing is expected to increase significantly, firms are capable to meet the increase through higher productivity of existing workers, rather than by creating new jobs and increasing work force.
A second factor expected to cause some employment declines in machinery manufacturing is the growing number of imported parts. Earlier only raw material was available now finish part machined and finished are also available and raw material suppliers are supplying the same to compete with the competition. This industry is less likely to lose a large part of its output to imports from other countries than some other manufacturing industries. The large size and complexity of many of the types of machinery made by this industry and the relatively skilled workforce it requires is an advantage that many manufacturing industries do not share.
The manufacturing focus in the early-to-mid-2000s was on new and diverse products to meet the individual needs and desires of the market. Companies in 2003 wanted "quick changeover capabilities, flexibility, and fast speeds" more than any other features. Consequently, the industry was expecting continued growth to meet demands for newer and better packaging machinery, replacing older equipment with newer, faster, more efficient, and more automated machines. Trends toward lightweight, individually designed, flexible, and reusable packaging increased demand for the design of machines that could manufacture such packaging.
Demand for machinery is expected to remain strong. Machinery is important for all industries because it boosts their productivity, and advances in technology will make machinery even more efficient and thus more desirable. Demand for machinery is highly sensitive to cyclical swings in the economy, however, causing employment in machinery manufacturing to fluctuate. During periods of economic prosperity, companies invest in new equipment, such as machinery, in order to boost production. When economic growth slows, however, many companies are reluctant to purchase new machinery. These changes in demand cause machinery manufacturers to replace fewer workers who leave or even lay off some workers.
Although overall employment in the machinery manufacturing industry is expected to decline, the outlook for occupations will vary; some will experience larger declines than others, while some will even experience growth instead. Increased automation and more efficient production processes will cause employment declines in assembler and fabricator occupations. Office and administrative support workers will also experience declines as a result of increased automation and contracting out. Employment in professional and management occupations will experience smaller declines relative to other occupations in the industry; engineers in particular will experience very good employment opportunities, as they are responsible for increasing innovation and competitiveness in the industry.
USE OF PROCESS & PACKAGING MACHINERY
Primary use of process and packaging machinery is to elated equipment and it's uses.
BLENDING & MIXING
Blending is to combine or mix so that the constituent parts are indistinguishable from one another and to obtain a mixture of particular character, quality or consistency. Blending machines such as Agitators, Conical blenders, Continuous mixers, Dough mixers, Emulsifiers, Gas, Homogenizers, In line mixers, Meat mixers, Paste mixers, Plough blade, Powder mixers, Ribbon mixers, Solid phase mixers, Viscous product mixers, Z Blade mixers.
GRANULATORS
Current good manufacturing practices increasingly require that product is fully contained during processing to protect operators and environment. Integrated process systems not only offer containment but improved productivity through automation, increased yield and efficient cleaning procedures. The granulation process can be one of the following; Low shear dry granulation, high shear wet granulation and melt granulating. Mixing and granulating can be combined into one machine.
HOMOGENIZERS
Homogenizer is to reduce to particles and disperse throughout a fluid. Inline homogenizers are the ideal solution for continuous processing of emulsions and dispersions.
MILLING & SIEVING
The integration of all types of mills and sieves can be tailored to suit the individual needs. There can be specific applications such as hoist mounted systems and high powder containment levels. Other design options include nitrogen purge systems and CIP systems. Quick change over between products is essential and the application of integrated control systems is needed. There are various types of mills such as toothed colloid, corundum stone and perforated disc mills. Product is loaded via a hopper that can also be fitted with a feed screw, or via a pump. The milling zone is sealed by a single or double-acting mechanical seal, with no dead space. All product contact surfaces should be very easily cleaned with no need for dismantling (CIP). Thorough washing of all static seals during the cleaning process complies with the hygiene standards. In all industrial sectors, demands in terms of flexibility and hygiene management are constantly on the increase.
POWDER HANDLING
Common problems include material blockages where sticky poor flowing materials will not discharge from an IBC. Segregation of blended material is another common problem. Segregation can be caused during the discharge from the IBC. It can also occur after discharge from the IBC when product is allowed to fall through long chutes in free fall, and displaced air from below is forced back up the chute and separates the finer particles from the coarser particles.
PROCESS VESSELS
Processing vessels need to be of a high quality construction and are widely used by the food and processing industries. A selection of sizes, specifications and agitator combinations are available to suit most needs. Stainless steel is used for all fabricated parts to meet industry requirements. Pressurized jackets for heating by steam or water facilitate boiling, cooking, melting, dispersion and mixing of products. Vessels can also be equipped for oil heating or water cooling.
IBC / INDUSTRIAL BULK CONTAINER
Container blending has long been established as the most efficient method of blending granules and powders in the pharmaceutical manufacturing process. Reduced loading and unloading times, reduced cleaning time of both machinery and room, improved containment and batch integrity have established IBC blending as the pharmaceutical industry’s technology of choice.
PROCESS PUMPS
Various types of process pumps can be used depending upon the type of product to be moved between or within the complete process line of the various integrated sub systems. Pumps such as centrifugal, diaphragm, dosing, gear, metering, reciprocation and vacuum can be used. For example, vacuum pumps will be used for powder handling but screw metering drives can be used for more accurate powder movement.
PROCESS CLEANING MACHINES
The cleaning of the process machines will be mainly carried out by CIP (Clean In Place) systems. Depending on the sensitivity of the product being produced, the equipment may be cleaned aseptically and therefore eliminating any possible contamination from outside.
STERILIZING MACHINES
Sterilizing machines can also be called, Autoclaves and Retorts. There three main types of sterilizing system; static, rotary and pilot or laboratory systems.
GENERAL CHARACTERISTICS ARE:-
• Steam-Water sprays mix.
• Top shower for cans and glass jars plus side shower for pouches and trays
• Indirect cooling system by heat exchanger allows water recovery.
• All vessel, pipe work and valves and heat exchanger in stainless steel materials
• Insulated shell with mirror polished stainless steel cladding
• PLC control with modem connection allows remote troubleshooting and servicing
• Process monitoring in the operator interface with complete information of temperature, pressure, time and flow
• Easy product recipe setup with password protected access
• Optimum heat distribution (+/-0,5 ยบC)
• Accurate pressure control (+/- 0,05 bar)
The rotary machines will use inverter drives for accurate control during the sterilizing process. There is also associated equipment such as basket trolleys and automatic loading systems available to fully automate the sterilizing process of product.
PROCESS CONTROL SYSTEMS
Compliance, traceability, consistency, and reliability of measurement data are primary concerns for the pharmaceutical industry. The control system is needed to verify the product quality through measuring, counting, inspection and testing of the manufacturing process. Operator input data; scanning systems and feedback systems are used.
PROCESS AND PACKAGING MACHINERY IN GENERAL
These machine types are very general indeed. Each area or sector of packaging equipment can be expanded upon to reveal the various applications that are available today. As technology advances, packaging machines are becoming more and more advanced to not only meet the current demands but to try and "future proof" the packaging equipment and product development within an organization. This can have a bearing on machine costs plus the interchangeability of operators and training. Packaging machines can be integrated into an existing line to enhance the production output or to reduce the labor and down type to pack the product. From single machine, to small systems or complete lines containing more than one new or existing / reconditioned packaging machine can be installed. Depending on the size of the installation, project process line and packaging machinery are available domestically to withstand & compete with market requirements.
FLEXIBLE PACKAGING TECHNOLOGY
FLEXIBLE PACKAGING TECHNOLOGY
Packaging is the science, art and technology of enclosing or protecting products for distribution, storage, sale, and use. Packaging also refers to the process of design, evaluation, and production of packages. Packaging can be described as a coordinated system of preparing goods for transport, warehousing, logistics, sale, and end use. Packaging contains, protects, preserves, transports, informs, and sells. In many countries it is fully integrated into government, business, and institutional, industrial, and personal use.
Package design and development are often thought of as an integral part of the new product development process. Alternatively, development of a package or component can be a separate process, but must be linked closely with the product to be packaged. Package design starts with the identification of all the requirements: structural design, marketing, shelf life, quality assurance, logistics, legal, regulatory, graphic design, end-use, environmental, etc. The design criteria, time targets, resources, and cost constraints need to be established and agreed upon.
Most packing systems use steam or superheated water to cook food in its own package, extending shelf life and ensuring food safety. Flexible packaging is not new. In fact, it has been around since the late 1960s when the Army began looking to replace its unpopular canned C-rations. That project led directly to Meal Ready to Eat (MRE) packaging, which the Army uses to this day. Since then, Flexible more economical, easy to pack, packaging has evolved from a mostly aluminum foil structure to a sophisticated multilayer, high barrier laminate package. The military, like most entrenched bureaucracies, is resistant to change. But there was virtually no resistance to the rapid adoption of the MRE. Why? Because food packaged in these flexible pouch tastes much better than canned rations.
PACKAGING
There is a saying in the packaging industry to the effect that "everybody thinks he is an expert on the subject." The implication of this judgment is that, of course, "they don't know the half of it." The public is intensely exposed to packaging, and its members will of course have an opinion, indeed an informed opinion. At the same time packaging is a vast subject extending deep in one direction to very hidden and sophisticated areas of materials science, in another into the protection of public health and welfare; it is the pillar supporting at least three major industries (paper and board, plastics, and glass); it is fought over by people who want to use its labels for disclosure and those who want "truth in advertising"; it is a very important branch of marketing and also of design activities; it is in itself a large and expensive industrial activity sometimes separate from production, placed at its end, sometimes integrated into the manufacturing process; it has its major subdivision of portion packaging, packaging, and outer packaging or packing; everything rides on its pallets; it is an important aspect of transportation, warehousing, and distribution generally; the word is used symbolically to mean "the artful presentation" of something, such as the "packaging" of a celebrity; finally, spent packaging is the bulk of solid waste and carelessly discarded packaging that is the litter of any country.
PACKAGING BASICS
Packaging divides into bulk, product, and portion packaging. Bulk packaging takes the form of cardboard boxes (much more rarely crates) and the pallets that carry these; it is intended to protect and is rarely ever used to advertise (except the maker of the box itself); even automobiles have bulk packaging in the form of protective sheets attached to windshields and other external features. Product packaging typically has two roles: protection and communication. The communication may be promotional, a service to the user (menus, preparation instructions), or a labeling requirement. The chief purpose of portion packaging is to deliver convenience—although such packaging also carries a message.
The producer needs to balance various aspects of a packaging system. In roughly the following order of importance, these are product protection, good production fit, low cost, and exploitability for marketing. To be sure, the package itself, first of all, must meet whatever regulations apply. Product protection includes basic product integrity and includes as long a shelf life as possible. The producer will prefer a system that permits rapid and efficient production with the lowest packaging equipment and packaging material costs. When given a choice, the surfaces should display the producer's messages as attractively as possible.
From the consumer's point of view, the ideal package will be easy to store, to open, and to close. It should be safe. It should carry warnings. If the product requires assembly or instructions to use, information should be present, and it should be clear. Consumers, of course, use brand identifications to choose products, but their strongest interest is in objective information carried on the labels, one reason why Congress has moved, in response, to require such labeling. People want to know what they are buying: Is it wool or polyester? How long will this half-and-half last? Can I use this as a diabetic? All else equal, the consumer also will prefer a package that can be reused in some way.
HISTORY
While there are many polymers utilized in the Flexible Packing Industry, the most common are polypropylene (PP), Polyethylene (PE), polyvinyl chloride (PVC), polyethylene terephthalate (PET), and Biaxially oriented polypropylene (BOPP)
Polyvinyl chloride (PVC)
Through initially created in 1872, PVC was not patented until 1913 by Friedrich Klatte. When PVC was plasticized in 1926, it was not long after it began to widely gain popularity in packing. With good cling and barrier properties, along with good heat seal properties; PVC is often used in the manufacturing of films for meats and produce as well as being a popular choice of blister packs. In recent years PVC has received negative attention from environmentalists, and very little growth is expected in the future.
Polyethylene (PE)
In 1933, PE was discovered by E. W. Fawcett and R. O. Gibson at the British Company Imperial Chemical Industries. After a reaction occurred between ethylene and benzldehyde, the substance that was left behind ultimately became polyethylene (The History of Plastic). Polyethylene later progressed to become three variations of itself –
a. High Density Polyethylene (HDPE)
b. Low Density Polyethylene (LDPE)
c. And Linear Low Density Polyethylene (LLDPE)
HDPE, LEPE and LLDPE are used in flexible packing applications due to their flexibility, good low temperature performance durability, high moisture barrier, and ability to seal to itself without any coating. PE is by far the most used plastic film materal that is used in flexible packing, and its growth is around 1.5% a year for European countries.
Polyethylene Terephthalate (PET)
In 1941 came PET. At the Calico Printers Association in Manchester, England, Rex Whinfield and James Dickson furthered research that had previously been done by Wallace Carothers (Bellis). PET possessed excellent high temperature properties, high strength and clarity, and has high oxygen and carbon dioxide barrier properties. Often used for medical application pouches, boil in bag applications, meat, snack, and baked goods, PET is an important player in the field of flexible packaging.
Polypropylene (PP)
In 1950 Paul Hogan and Robert Banks, both of whom were working for Phillips Petroleum, were ultimately credited with the invention of PP (A Plastic Explosion Polyethylene, Polypropylene, and others) After finding that modification of their original catalyst of nickel oxide to include chromium oxide, the chromium produced a material polypropylene. PP is commonly used in moisture proof wrapping, fat resistant films, and in the manufacture of medical packing due to low moisture absorption high chemical resistance and low permeability to moisture.
EVOLUTION
Packaging is nothing new and predates modern times, but the form it takes is a direct reflection of settlement patterns, the reach of the economy, food preservation technology, and the nature of the transportation system. Before the modern era took serious hold after World War I, only a few products were packaged. Canning dates back to the days of Napoleon, some of whose formations, marching into Russia, received canned goods in newly invented tin-lined metal cans. Other long-lasting products (what today we call long shelf-life products), like hard biscuits and cookies, were packaged; chocolates and candies came in fancy boxes as well. Perfumes were an early and highly visible packaged product. All of these, and others, from the very beginning, bore brand identifications. Many small products like buttons and needles were prepackaged. Packaging initially served the needs and convenience of the seller; the package itself became a container in the consumer's home. Urban settlement was dense. Refrigeration was not yet wide-spread. Food shopping took place daily. People took milk or oil cans to the store to have them filled; preserves came in glass that could be recycled; paper packaging was used, often made on the spot from sheets by the merchant; the "shopping basket" itself was the generic carrier of groceries. Long distance packing used to be in crates fashioned of wood. Of that technology today only the wood pallet survives.
Packaging technology saw intense development immediately before and during World War II in efforts to supply the fighting forces—and not just those of the Mass distribution of packaged products began and then continued thereafter. Sturdy Kraft paper, two outer layers reinforced by a corrugated inner layer (the corrugated box) took over bulk packaging. Milk began to transit from recyclable glass bottles to paper containers initially coated with wax and then, after the war, by hot melt plastics, a combination of wax and plastics. Plastics saw an immense expansion in the 1950s and 60s; polyethylene became a staple of flexible packaging, polyvinyl chloride (PVC) became a standard form of transparent packaging, and polyurethane foam plastics came to dominate a field that had once belong to pressed paper pulp. Composite materials (laminates) became possible as a consequence of the emergence of high-performance adhesives. Packaging grew stronger, lighter, and easier to process by machine. Aluminum entered the beverage market as aluminum cans and also as easy-open closures for steel cans. As mass production developed in the underlying materials, and forming and packaging machinery became ever more affordable, many products not heretofore packaged were now "shrink-wrapped" onto sheets of cardboard, bagged, and boxed. In parallel with the physical development of packaging, companies exploited the surfaces of packaging to print their brand names and messages, a process aided by rapidly advancing printing technology and improved inks. The potential of using the package itself as a means of differentiation or a means of delivering convenience (the single-cup tea bag, the single-serving ketchup package) rapidly created a brand-new dimension in packaging. Packaging and marketing began to merge. Packaging grew in total volume to such an extent that by the 1970s it began to attract government attention as a new cost imposed on waste disposal systems. Discarded packaging—particularly after cans took over beer and soft drink distribution from recyclable bottles—produced deposit legislation aimed at curbing litter.
By the 1970s packaging had reached maturity and has since evolved less dramatically and visibly. However, the underlying materials sciences are still producing ever better and ever more specialized and differentiated packaging. As the early 2000s advance, the protective capacities of packaging are improving so that some heretofore refrigerated products are available on ordinary shelves and others will likely follow. New composites are announced every year. Competition between materials continues; costlier materials like metals, paper, and glass are everywhere pressed by plastics; this trend, however, may reverse if the price of oil (the source of plastics) keeps climbing. Strange and wonderful extensions of the packaging-marketing synthesis are being talked about, like imprinting fresh fruit with messages adhering to microscopically thin coatings.
The continuing evolution of packaging at a technical level serves as an indicator that, despite much hype about the package as a promotional vehicle, the predominant function of packaging in the economy is product protection first, convenience next. The consumer also values objective information. Functionally, the hype comes last.
PACKAGING AS A BUSINESS FUNCTION
It is clear from the discussion thus far that packaging, for the business owner, touches all aspects of the business. All depending on the product, of course, it may involve significant engineering work to ensure fit with the production process, satisfy legal requirements regarding safety, yet incorporate the aesthetics chosen for product promotion. Packaging often involves aggregation of multiple units into one package. The optimal package cost for the right aggregate has to be priced properly to achieve desired volume while fitting vendors' shelf space. Product aesthetics must accommodate legal labeling requirements. Different modes of packaging will deliver higher and lower out-of-pocket costs but may produce harder-to-predict sales volumes.
These problems tend to sort out reasonably well because a great variety of analogous cases exist in the market to suggest which general model to follow—or which edge of which envelope to push. Packaging is a large and sophisticated industry, and the small business owner will be able to identify both package designers and suppliers of packaging equipment easily enough. Designers typically know the equipment available; conversely, packaging equipment suppliers can recommend designers they work with routinely.
LABELING: CONSUMERS WANT IT
The Fair Packaging and Labeling Act of 1966 regulate packaging and labeling. The act requires that every product package specify on its "principal display label"—that part of the label most likely to be seen by consumers—the following information:
1) The product type;
2) The producer or processor's name and location;
3) The quantity (if applicable); and
4) The number and size of servings (if applicable).
Furthermore, several restrictions apply to the way that the label is displayed. For example, mandatory copy required by the act must be in boldface type. Also, if the company is not listed in the telephone book, the manufacturers or importer's street address must be displayed.
NEW GENERATION PACKING
The latest generation of flexible packaging has a pervasive theme: convenience. Pouches and bags for foods in a variety of categories showcase refinements in ease of package handling and opening as well as product access and preparation.
Consumer demand for fast, easy cooking continues to be a major driver. In the frozen-foods segment, for a flexible package with steam-in-pack functionality for its new line of frozen mashed potatoes, use of a steam-in-package structure, a package concept that has rapidly gained momentum in the past two years. Bags made from a laminate of polyethylene terephthelate (PET) and polypropylene. A high-performance sealant on the interior of the laminated film enables the packaging material to perform well in the full range of temperatures associated with frozen distribution and microwave cooking. In other categories, brand owners are opting for packaging with easy-open features that make portion control and product access easier. The serrated edge of the back seal creates a series of tear initiation points along the longitudinal edge of the package. Thus on-the-go consumers can easily share the product or save part of it to eat later, all without touching the product. A stand-up pouch designed with a wide opening for easy product access is finding applications for snacks and produce. The stackable pouch features a top and bottom gusset; the top gusset is scored on the interior of the package. To open the pouch, the consumer applies pressure along the score line and pushes the sides of the top gusset to the sides of the pouch. The blueberries can be consumed directly from the pack, and they may be washed in the package thanks to holes incorporated in the bottom of the pouch. This package format, called the PushPop. Applications for the film include formed packages, wrap-around labels, in-mold labels and thermoformed labels. According to the supplier, the film is compatible with sealing, printing, embossing, die cutting and machining. In addition to keeping food hot or cold, packaging made from the film would insulate consumers’ hands from the temperature extremes of items such as ice cream, soup and hot beverages.
Foods, toys, drugs, cosmetics, furs, and textiles require special labeling. Under the act, the label for edible products, for example, must provide sodium content if other nutritional information is also shown. Labels must also show ingredients, in descending order from the one of highest quantity to the one of least quantity. Certain food items, such as beef, may also be required to display qualitative "grade labels" or inspection labels. Likewise, "informative labeling" may be required for products such as home appliances. Informative label requirements mandate information about use, care, performance capability, life expectancy, safety precautions, gas mileage, or other factors. Certain major home appliances, for example, must provide the estimated cost of running each make and model for one year at average utility rates.
Regulatory Authorities have passed significant new labeling legislation, the Nutrition Labeling and Education Act of 1990; the act became effective in the mid-1990s. This act is intended primarily to discourage misleading labeling related to health benefits of food items. Specifically, many package labels subjectively claimed that their contents were "low-fat," "high-fiber," or possessed some other health virtue when the facts indicated otherwise. Basically, the new laws require most food labels to specify values such as calorie and cholesterol content, fat and saturated fat percentages, and sodium levels.
FUTURE INNOVATIONS
Looking to the future of flexible films, there are already foreseen consumer and development trends as well as continuing innovations in the field. An ongoing trend is the packing market is the development of materials which posses high barrier properties. There is continuing research regarding biodegradable / compostable films (There have been launches of biodegradable films such as the bio based film released by Alcan in early 2008) and the push to make them more widely available and utilized. A recent application of Food grade flavor molecules added to polymer structure has resulted in the development of a film that releases odors / aromas on the inside or outside of a package. The flexible film industry has been the centre of revolutionary developments and innovations, both of which will cease anytime soon.
The flexible packing industry is the second largest in the packaging segment. From the start of the creation of popular modern polymers, to the manufacturing practices used to create plastic films, to the ongoing developments in the field, flexible films have been able to continually grow, expand, and provide packing engineers with endless possibilities.
With the constant research and development surrounding flexible films, it is safe to assume that there will continue to be modifications to the existing materials as well as innovational additions to the already expansive flexible film field. It is through these innovations that, makes our products, protect, preserve and present as we see the world around us.
Nanotechnology is a cross-sectional technology, and it will play an important future rule in almost all areas of technical developments. Nanotechnology has become the focus of immense expectations in terms of market potential and efficiency. Although there has been a plethora of start-up companies, research funding, and even several highly publicized commercial successes, the early market expectations have not been realized, and many are wondering how big the gap is between fantasy and reality.
Packaging is a relatively large and important application for nanotechnology. Materials constructed from nanotechnology have been found to provide unexpected and valuable packaging properties. These properties may even be of such high value that they can justify the early price of nano-materials. More to be enhanced will be properties of such nano-materials, its barrier properties, its bulk mechanical propertied, it flame durability, biodegradability, product identification, color and order responses, Electrical and thermal conductivity. Components and manufacture of a nano-composite material like nano-fibers, nano clay, and nano-oxides are also a part of study as future awaits innovation for the flexible packing industry.
Packaging is the science, art and technology of enclosing or protecting products for distribution, storage, sale, and use. Packaging also refers to the process of design, evaluation, and production of packages. Packaging can be described as a coordinated system of preparing goods for transport, warehousing, logistics, sale, and end use. Packaging contains, protects, preserves, transports, informs, and sells. In many countries it is fully integrated into government, business, and institutional, industrial, and personal use.
Package design and development are often thought of as an integral part of the new product development process. Alternatively, development of a package or component can be a separate process, but must be linked closely with the product to be packaged. Package design starts with the identification of all the requirements: structural design, marketing, shelf life, quality assurance, logistics, legal, regulatory, graphic design, end-use, environmental, etc. The design criteria, time targets, resources, and cost constraints need to be established and agreed upon.
Most packing systems use steam or superheated water to cook food in its own package, extending shelf life and ensuring food safety. Flexible packaging is not new. In fact, it has been around since the late 1960s when the Army began looking to replace its unpopular canned C-rations. That project led directly to Meal Ready to Eat (MRE) packaging, which the Army uses to this day. Since then, Flexible more economical, easy to pack, packaging has evolved from a mostly aluminum foil structure to a sophisticated multilayer, high barrier laminate package. The military, like most entrenched bureaucracies, is resistant to change. But there was virtually no resistance to the rapid adoption of the MRE. Why? Because food packaged in these flexible pouch tastes much better than canned rations.
PACKAGING
There is a saying in the packaging industry to the effect that "everybody thinks he is an expert on the subject." The implication of this judgment is that, of course, "they don't know the half of it." The public is intensely exposed to packaging, and its members will of course have an opinion, indeed an informed opinion. At the same time packaging is a vast subject extending deep in one direction to very hidden and sophisticated areas of materials science, in another into the protection of public health and welfare; it is the pillar supporting at least three major industries (paper and board, plastics, and glass); it is fought over by people who want to use its labels for disclosure and those who want "truth in advertising"; it is a very important branch of marketing and also of design activities; it is in itself a large and expensive industrial activity sometimes separate from production, placed at its end, sometimes integrated into the manufacturing process; it has its major subdivision of portion packaging, packaging, and outer packaging or packing; everything rides on its pallets; it is an important aspect of transportation, warehousing, and distribution generally; the word is used symbolically to mean "the artful presentation" of something, such as the "packaging" of a celebrity; finally, spent packaging is the bulk of solid waste and carelessly discarded packaging that is the litter of any country.
PACKAGING BASICS
Packaging divides into bulk, product, and portion packaging. Bulk packaging takes the form of cardboard boxes (much more rarely crates) and the pallets that carry these; it is intended to protect and is rarely ever used to advertise (except the maker of the box itself); even automobiles have bulk packaging in the form of protective sheets attached to windshields and other external features. Product packaging typically has two roles: protection and communication. The communication may be promotional, a service to the user (menus, preparation instructions), or a labeling requirement. The chief purpose of portion packaging is to deliver convenience—although such packaging also carries a message.
The producer needs to balance various aspects of a packaging system. In roughly the following order of importance, these are product protection, good production fit, low cost, and exploitability for marketing. To be sure, the package itself, first of all, must meet whatever regulations apply. Product protection includes basic product integrity and includes as long a shelf life as possible. The producer will prefer a system that permits rapid and efficient production with the lowest packaging equipment and packaging material costs. When given a choice, the surfaces should display the producer's messages as attractively as possible.
From the consumer's point of view, the ideal package will be easy to store, to open, and to close. It should be safe. It should carry warnings. If the product requires assembly or instructions to use, information should be present, and it should be clear. Consumers, of course, use brand identifications to choose products, but their strongest interest is in objective information carried on the labels, one reason why Congress has moved, in response, to require such labeling. People want to know what they are buying: Is it wool or polyester? How long will this half-and-half last? Can I use this as a diabetic? All else equal, the consumer also will prefer a package that can be reused in some way.
HISTORY
While there are many polymers utilized in the Flexible Packing Industry, the most common are polypropylene (PP), Polyethylene (PE), polyvinyl chloride (PVC), polyethylene terephthalate (PET), and Biaxially oriented polypropylene (BOPP)
Polyvinyl chloride (PVC)
Through initially created in 1872, PVC was not patented until 1913 by Friedrich Klatte. When PVC was plasticized in 1926, it was not long after it began to widely gain popularity in packing. With good cling and barrier properties, along with good heat seal properties; PVC is often used in the manufacturing of films for meats and produce as well as being a popular choice of blister packs. In recent years PVC has received negative attention from environmentalists, and very little growth is expected in the future.
Polyethylene (PE)
In 1933, PE was discovered by E. W. Fawcett and R. O. Gibson at the British Company Imperial Chemical Industries. After a reaction occurred between ethylene and benzldehyde, the substance that was left behind ultimately became polyethylene (The History of Plastic). Polyethylene later progressed to become three variations of itself –
a. High Density Polyethylene (HDPE)
b. Low Density Polyethylene (LDPE)
c. And Linear Low Density Polyethylene (LLDPE)
HDPE, LEPE and LLDPE are used in flexible packing applications due to their flexibility, good low temperature performance durability, high moisture barrier, and ability to seal to itself without any coating. PE is by far the most used plastic film materal that is used in flexible packing, and its growth is around 1.5% a year for European countries.
Polyethylene Terephthalate (PET)
In 1941 came PET. At the Calico Printers Association in Manchester, England, Rex Whinfield and James Dickson furthered research that had previously been done by Wallace Carothers (Bellis). PET possessed excellent high temperature properties, high strength and clarity, and has high oxygen and carbon dioxide barrier properties. Often used for medical application pouches, boil in bag applications, meat, snack, and baked goods, PET is an important player in the field of flexible packaging.
Polypropylene (PP)
In 1950 Paul Hogan and Robert Banks, both of whom were working for Phillips Petroleum, were ultimately credited with the invention of PP (A Plastic Explosion Polyethylene, Polypropylene, and others) After finding that modification of their original catalyst of nickel oxide to include chromium oxide, the chromium produced a material polypropylene. PP is commonly used in moisture proof wrapping, fat resistant films, and in the manufacture of medical packing due to low moisture absorption high chemical resistance and low permeability to moisture.
EVOLUTION
Packaging is nothing new and predates modern times, but the form it takes is a direct reflection of settlement patterns, the reach of the economy, food preservation technology, and the nature of the transportation system. Before the modern era took serious hold after World War I, only a few products were packaged. Canning dates back to the days of Napoleon, some of whose formations, marching into Russia, received canned goods in newly invented tin-lined metal cans. Other long-lasting products (what today we call long shelf-life products), like hard biscuits and cookies, were packaged; chocolates and candies came in fancy boxes as well. Perfumes were an early and highly visible packaged product. All of these, and others, from the very beginning, bore brand identifications. Many small products like buttons and needles were prepackaged. Packaging initially served the needs and convenience of the seller; the package itself became a container in the consumer's home. Urban settlement was dense. Refrigeration was not yet wide-spread. Food shopping took place daily. People took milk or oil cans to the store to have them filled; preserves came in glass that could be recycled; paper packaging was used, often made on the spot from sheets by the merchant; the "shopping basket" itself was the generic carrier of groceries. Long distance packing used to be in crates fashioned of wood. Of that technology today only the wood pallet survives.
Packaging technology saw intense development immediately before and during World War II in efforts to supply the fighting forces—and not just those of the Mass distribution of packaged products began and then continued thereafter. Sturdy Kraft paper, two outer layers reinforced by a corrugated inner layer (the corrugated box) took over bulk packaging. Milk began to transit from recyclable glass bottles to paper containers initially coated with wax and then, after the war, by hot melt plastics, a combination of wax and plastics. Plastics saw an immense expansion in the 1950s and 60s; polyethylene became a staple of flexible packaging, polyvinyl chloride (PVC) became a standard form of transparent packaging, and polyurethane foam plastics came to dominate a field that had once belong to pressed paper pulp. Composite materials (laminates) became possible as a consequence of the emergence of high-performance adhesives. Packaging grew stronger, lighter, and easier to process by machine. Aluminum entered the beverage market as aluminum cans and also as easy-open closures for steel cans. As mass production developed in the underlying materials, and forming and packaging machinery became ever more affordable, many products not heretofore packaged were now "shrink-wrapped" onto sheets of cardboard, bagged, and boxed. In parallel with the physical development of packaging, companies exploited the surfaces of packaging to print their brand names and messages, a process aided by rapidly advancing printing technology and improved inks. The potential of using the package itself as a means of differentiation or a means of delivering convenience (the single-cup tea bag, the single-serving ketchup package) rapidly created a brand-new dimension in packaging. Packaging and marketing began to merge. Packaging grew in total volume to such an extent that by the 1970s it began to attract government attention as a new cost imposed on waste disposal systems. Discarded packaging—particularly after cans took over beer and soft drink distribution from recyclable bottles—produced deposit legislation aimed at curbing litter.
By the 1970s packaging had reached maturity and has since evolved less dramatically and visibly. However, the underlying materials sciences are still producing ever better and ever more specialized and differentiated packaging. As the early 2000s advance, the protective capacities of packaging are improving so that some heretofore refrigerated products are available on ordinary shelves and others will likely follow. New composites are announced every year. Competition between materials continues; costlier materials like metals, paper, and glass are everywhere pressed by plastics; this trend, however, may reverse if the price of oil (the source of plastics) keeps climbing. Strange and wonderful extensions of the packaging-marketing synthesis are being talked about, like imprinting fresh fruit with messages adhering to microscopically thin coatings.
The continuing evolution of packaging at a technical level serves as an indicator that, despite much hype about the package as a promotional vehicle, the predominant function of packaging in the economy is product protection first, convenience next. The consumer also values objective information. Functionally, the hype comes last.
PACKAGING AS A BUSINESS FUNCTION
It is clear from the discussion thus far that packaging, for the business owner, touches all aspects of the business. All depending on the product, of course, it may involve significant engineering work to ensure fit with the production process, satisfy legal requirements regarding safety, yet incorporate the aesthetics chosen for product promotion. Packaging often involves aggregation of multiple units into one package. The optimal package cost for the right aggregate has to be priced properly to achieve desired volume while fitting vendors' shelf space. Product aesthetics must accommodate legal labeling requirements. Different modes of packaging will deliver higher and lower out-of-pocket costs but may produce harder-to-predict sales volumes.
These problems tend to sort out reasonably well because a great variety of analogous cases exist in the market to suggest which general model to follow—or which edge of which envelope to push. Packaging is a large and sophisticated industry, and the small business owner will be able to identify both package designers and suppliers of packaging equipment easily enough. Designers typically know the equipment available; conversely, packaging equipment suppliers can recommend designers they work with routinely.
LABELING: CONSUMERS WANT IT
The Fair Packaging and Labeling Act of 1966 regulate packaging and labeling. The act requires that every product package specify on its "principal display label"—that part of the label most likely to be seen by consumers—the following information:
1) The product type;
2) The producer or processor's name and location;
3) The quantity (if applicable); and
4) The number and size of servings (if applicable).
Furthermore, several restrictions apply to the way that the label is displayed. For example, mandatory copy required by the act must be in boldface type. Also, if the company is not listed in the telephone book, the manufacturers or importer's street address must be displayed.
NEW GENERATION PACKING
The latest generation of flexible packaging has a pervasive theme: convenience. Pouches and bags for foods in a variety of categories showcase refinements in ease of package handling and opening as well as product access and preparation.
Consumer demand for fast, easy cooking continues to be a major driver. In the frozen-foods segment, for a flexible package with steam-in-pack functionality for its new line of frozen mashed potatoes, use of a steam-in-package structure, a package concept that has rapidly gained momentum in the past two years. Bags made from a laminate of polyethylene terephthelate (PET) and polypropylene. A high-performance sealant on the interior of the laminated film enables the packaging material to perform well in the full range of temperatures associated with frozen distribution and microwave cooking. In other categories, brand owners are opting for packaging with easy-open features that make portion control and product access easier. The serrated edge of the back seal creates a series of tear initiation points along the longitudinal edge of the package. Thus on-the-go consumers can easily share the product or save part of it to eat later, all without touching the product. A stand-up pouch designed with a wide opening for easy product access is finding applications for snacks and produce. The stackable pouch features a top and bottom gusset; the top gusset is scored on the interior of the package. To open the pouch, the consumer applies pressure along the score line and pushes the sides of the top gusset to the sides of the pouch. The blueberries can be consumed directly from the pack, and they may be washed in the package thanks to holes incorporated in the bottom of the pouch. This package format, called the PushPop. Applications for the film include formed packages, wrap-around labels, in-mold labels and thermoformed labels. According to the supplier, the film is compatible with sealing, printing, embossing, die cutting and machining. In addition to keeping food hot or cold, packaging made from the film would insulate consumers’ hands from the temperature extremes of items such as ice cream, soup and hot beverages.
Foods, toys, drugs, cosmetics, furs, and textiles require special labeling. Under the act, the label for edible products, for example, must provide sodium content if other nutritional information is also shown. Labels must also show ingredients, in descending order from the one of highest quantity to the one of least quantity. Certain food items, such as beef, may also be required to display qualitative "grade labels" or inspection labels. Likewise, "informative labeling" may be required for products such as home appliances. Informative label requirements mandate information about use, care, performance capability, life expectancy, safety precautions, gas mileage, or other factors. Certain major home appliances, for example, must provide the estimated cost of running each make and model for one year at average utility rates.
Regulatory Authorities have passed significant new labeling legislation, the Nutrition Labeling and Education Act of 1990; the act became effective in the mid-1990s. This act is intended primarily to discourage misleading labeling related to health benefits of food items. Specifically, many package labels subjectively claimed that their contents were "low-fat," "high-fiber," or possessed some other health virtue when the facts indicated otherwise. Basically, the new laws require most food labels to specify values such as calorie and cholesterol content, fat and saturated fat percentages, and sodium levels.
FUTURE INNOVATIONS
Looking to the future of flexible films, there are already foreseen consumer and development trends as well as continuing innovations in the field. An ongoing trend is the packing market is the development of materials which posses high barrier properties. There is continuing research regarding biodegradable / compostable films (There have been launches of biodegradable films such as the bio based film released by Alcan in early 2008) and the push to make them more widely available and utilized. A recent application of Food grade flavor molecules added to polymer structure has resulted in the development of a film that releases odors / aromas on the inside or outside of a package. The flexible film industry has been the centre of revolutionary developments and innovations, both of which will cease anytime soon.
The flexible packing industry is the second largest in the packaging segment. From the start of the creation of popular modern polymers, to the manufacturing practices used to create plastic films, to the ongoing developments in the field, flexible films have been able to continually grow, expand, and provide packing engineers with endless possibilities.
With the constant research and development surrounding flexible films, it is safe to assume that there will continue to be modifications to the existing materials as well as innovational additions to the already expansive flexible film field. It is through these innovations that, makes our products, protect, preserve and present as we see the world around us.
Nanotechnology is a cross-sectional technology, and it will play an important future rule in almost all areas of technical developments. Nanotechnology has become the focus of immense expectations in terms of market potential and efficiency. Although there has been a plethora of start-up companies, research funding, and even several highly publicized commercial successes, the early market expectations have not been realized, and many are wondering how big the gap is between fantasy and reality.
Packaging is a relatively large and important application for nanotechnology. Materials constructed from nanotechnology have been found to provide unexpected and valuable packaging properties. These properties may even be of such high value that they can justify the early price of nano-materials. More to be enhanced will be properties of such nano-materials, its barrier properties, its bulk mechanical propertied, it flame durability, biodegradability, product identification, color and order responses, Electrical and thermal conductivity. Components and manufacture of a nano-composite material like nano-fibers, nano clay, and nano-oxides are also a part of study as future awaits innovation for the flexible packing industry.
BIOPHARMACEUTICAL & NANOTECHNOLOGY
BIOPHARMACEUTICAL & NANOTECHNOLOGY
In today’s technological age, it seems advancements in all fields leap forward by the day. Medical technology certainly hasn’t been left out of the loop, and some of the breakthroughs in modern medicine have been quite revolutionary and had a huge impact. But where will the field of medicine be in 20 years from now? What major advancements are waiting just around the next corner? In this article we will consider just two of the biggest technologies that are emerging over the horizon.
Electronic Implants
We have computers everywhere these days, but it’s not just the ones on our desks that we use to surf the net. We have computer chips in washing machines and just about all of our other appliances too. In the realm of science fiction (all too often a prediction of future science) we have seen technologically enhanced humans with superhuman abilities but what if those technologies were real and used for medical purposes?
Scientists have been working for years on implementing a special kind of microchip known as a “neuroprosthetic chip” that can be implanted into the brain. This chip helps to decipher signals in the brain when the brain itself cannot, and to trigger the appropriate responses. For example, the chip could help to control epileptic seizures, or help a patient suffering with paralysis to control prosthetic limbs with thought alone.
Stem Cell Research
One of the most talked about areas of medical technology today is stem cell research. With the first human trials currently taking place to determine the safety of human treatment, stem cell technology may not be too far away. The basis of stem cell therapy is regenerative: stem cells help the body to form new cells and generate tissue. If we can harness the power of stem cells for medical use, we may be able to cure paralysis, blindness, heart disease and diabetes, treat stroke patients and repair damaged organs and tissues, helping the body to regenerate and cure itself. Some people are even optimistic that stem cell research could lead to curing cancer!
Stem cell research has been the subject of much controversy. The needed stem cells are actually taken from embryos developed using IVF techniques as there are often surplus embryos and these are donated for scientific use. The stem cells gathered in this way are generic and have no predetermined cell type, which enables scientists to force the stem cells to become a specific, needed type of cell that can be injected into a patient in need of them. The embryos are only a few days old and about the size of a full stop (period), but there are many who think that stem cell research is just plain wrong; that it is “playing God” with an unborn child. This may all change as new research shed light on the ability to use adult stem cells, but only time will tell.
Nanomedicine
Nanotechnology, especially nanomedicine, are advancing significantly day by day. Nanoparticles are being already used in many products (mainly in cosmetics), but other spheres such as pharmaceutics and general medicine are slowly applying nanotechnology standards.
Nanomedicine, along with stem cells research, will probably change the way the world sees medicine. Many experts predict that it will change everything.
This was just a brief look at what the future of medicine may hold for us, but with these and many more exciting technologies rapidly emerging that future certainly looks bright.
BIOPHARMACEUTICAL
A biopharmaceutical is defined as a medical drug (proteins including antibodies, nucleic acids, DNA, RNA or antisense oligonucleotides) which is produced using biotechnology. In the late 1990s advances in manufacturing and processing revolutionized the production of biopharmaceuticals such as recombinant DNA technology and hybridoma technology. These technological advances have enabled the market place to open up and for smaller players to enter and capitalize on the growing need for targeted, personalized medicine.
During the 1960s and 1970s formulation began to assume greater importance. More recently still, the inconvenience of parenteral administration became a focus for attempts to minimize the burden and optimize treatment. Nowadays, any development programme for a new drug will include consideration of the optimal dosage form from the conception of a drug development project. A plethora of delivery platforms have evolved to meet market demands and overcome solubility and pharmacokinetic issues, and will have an important role to play in determining the dosage form that ultimately appears on the market.
The biopharm field represents a major opportunity for generic manufacturers with sufficient resources to withstand the relatively high development costs and the technological demand. It is estimated that biosimilars, targeting the six leading biopharm products, could generate revenues in excess of $2 billion within 2-3 years. However, there are considerable challenges facing companies developing and marketing biopharm products.
Manufacturing problems will remain a significant hurdle for companies entering this field; the regulation of innovator biopharm products continues to evolve and the harmonization of regulatory processes among the three main national regulatory agencies (the EU, the US and Japan) should make life simpler for biopharm companies seeking to establish a global presence for their products.
Biotherapeutics represent 7.5 percent of all drugs on the market; they account for approximately 10 percent of the total expenditure for marketed drugs and their use is growing at more than 20 percent per year. Biotechnology drug candidates account for around 32 percent of all pipeline research programs. In addition, biological drugs are administered in life-saving or end-stage applications, 74 percent more than chemically derived pharmaceuticals.
NANOTECHNOLOGY
Nanotechnology is the science of maneuvering and modifying the structure and properties of matter at an atomic and molecular scale. Due to these manipulations, inert elements start to function as catalyst, and insoluble matter develop unique solubility capacity. Likewise, non-colloids begin exhibiting excellent colloidal properties and electrical non-conductors start conducting electricity. All these materials can be used for a vast variety of purposes in field as diverse as medicine, energy production and electronics.
In recent years, nanotechnology has found innumerable applications in the field of medicine — from drug delivery systems, nano-robots and cell repair machines to imaging, nano-particles and nano-nephrology. Owing to the extensive use of nano-materials in medical equipments and devices, nano-medicine has become a significant branch of nanotechnology. Here are some important uses of nanotechnology in the field of medicine. All these things prove that nanotechnology will play a significant role in the future, and shows why nanotechnology is useful.
Drug Delivery System And Nanoparticles
The primary objective of the drug delivery system is to make the life-saving drug available in that part of the body where it is required the most. However, most of the time, these systems fail to work efficiently because the particles of the drug are too large for the cells to absorb, or they are insoluble or they have the potential to cause tissue damage. On the other hand, due to their exceedingly small size, nanoparticles are easily taken up by the cell. Moreover, they are completely soluble and they do not also damage the tissues. In nutshell, the efficiency of the drug delivery system can be increased several times by integrating nanoparticles with them.
Coupling Of Nanoparticles With Biopharmaceuticals
Biopharmaceuticals are peptides or protein molecules that trigger multiple reactions in the human body. They are widely used in the treatment of life-threatening diseases like cancer. The effectiveness of biopharmaceuticals can be increased several times by coupling them with nanoparticles, which will proficiently deliver the peptides or proteins at the tumor site and in this manner cure cancer without causing extensive damage to the adjacent tissues and organs.
Nanotechnology And Neuro-Electronic Devices
Neuro-electronic devices are unique machines based on nanotechnology that connect the nervous system with the computer. These devices not just detect and interpret the signals from the nervous system, but also control and respond to them. They can be used in the treatment of diseases that slowly and steadily decay the nervous system like multiple sclerosis.
Nanonephrology
This is a sub-branch of nanomedicine which is concerned with the detection and treatment of kidney diseases. Here various devices based on nanotechnology are used for the studying the different kidney processes and detecting disorders. Thereafter, nanoparticles and drug delivery system are used for curing the disorder.
Nanotechnology And Cell Repair Machines
These cell repair machines use nanotechnology to penetrate into the cell and rectify disorders like DNA damage or enzyme deficiency. These machines are no bigger than a bacteria or virus.
Nanorobots
The entry of nanorobots will literally revolutionize the world of medicine. These miniature devices would not only be capable of entering into the body and detecting the diseases and infection, but they will also be capable of repairing internal injuries and wounds.
Nanotech and Cancer
Nanotechnology deals with manipulating the structure as well as properties of matter at the atomic and molecular level. As the result of this maneuvering, the properties of matter change dramatically. While some insoluble elements develop high solubility capacity, inert substances start exhibiting catalyst properties. Owning to their size and properties, nanomaterials are extensively used for the treatment of a number of diseases. Cancer is such a disease where nanotechnology can play a significant role.
Nanoparticles And Nanorobots
Cancer is a condition where changes occur in a small percentage of cells and they start replicating interminably. Problems come to the fore only when the condition becomes unmanageable. The size of nanoparticles and nanorobots is exceedingly small, and because of this property, they can easily enter into the blood vessels, organs, tissues and even the cells of the body. Additionally, they can also find out those cells that are growing abnormally. Thus, they can play a decisive role in the detection of cancer at a very early stage.
Accurate Drug Delivery
Once the cancer has been detected, it becomes essential to treat it as quickly as possible. Most of the cancer treatment methods cause widespread damage because while eliminating the cancerous cells they also start acting upon the normal cells. Drug delivery systems that use nanoparticles can effectively treat cancer without damaging the surrounding cells and tissues. These nanoparticles are smaller than the body cells, and can easily carry the drug to that part of the body where the cancerous cells are located.
Biopharmaceuticals And Cancer
Biopharmaceuticals are basically proteins molecules that trigger multiple reactions in the human body. They are widely used in the treatment of cancer. The effectiveness of these pharmaceuticals will increase several times if they are coupled with nanoparticles. The nanoparticles will carry the biopharmaceuticals directly to the tumor site without adversely affecting the cells and tissues that come in the way. In this manner, cancer would be cured and healthy cells will remain as such.
Cell Repair Machine And Cancer Treatment
Cancer primarily occurs due to mutation; the genetic information stored in the DNA is changed. As the result the affected cells divide continuously and cause the formation of tumors. The cell repair machine that is as small as a nanoparticle can easily penetrate into the cancerous cell and repair the damaged DNA. As the technique is completely non-invasive, therefore the normal cells remain unharmed.
HISTORY OF NANOTECHNOLOGY
In 1974, Norio Taniguchi of the Tokyo Science University, defined the term nanotechnology for the first time. According to his definition, nanotechnology encompasses separating, processing, consolidating and deforming matter at atomic and molecular scales. Although the term nanotechnology got its definition in 1974, the actual concept was introduced way back in 1867, when James Clerk Maxwell proposed a minuscule entity called Maxwell’s Demon that was capable of handling individual molecules.
Richard Adolf Zsigmondy was the first person to observe and measure the dimensions of nanoparticles. He was also the first person to use nanometer for characterizing the size of the nanoparticles unambiguously. He determined that 1 nm was 1/1,000,000 millimeter. He also developed the first classification system that was based on size of the particle that ranged in nanometer.
In the 20th century several developments took place that helped in characterizing nanomaterials. Like in 1920, Irving Langmuir introduced the concept of monolayer, where a layer of material is just one molecule thick. He received a Nobel Prize for this concept.
In 1959, Richard Feynman, at a meeting of American Physical Society at Caltech, put forth a process that had the ability to control and modify individual atoms and molecules. He stated that by scaling down the dimensions of the atom, dramatic changes can be brought about in its properties. After the discourse, he announced two challenges; first was the construction of nanomotor, which achieved by William McLellan in 1960,and second involved the process of scaling down the letters of Britannica Encyclopedia to fit on the head of a pin; this task was accomplished by Tom Newman in 1985.
In 1965, Gordon Moore made an astounding prediction; he stated that the number of transistors that could fit in a specific area would double every 18 years for the next 10 years. Till this date the trend is continuing, from 2000 transistors in 4004 processors to 7,000,000,000 transistors in Core 2, and Gordon’s prediction is popularly known as Moore’s Law.
In 1974, Dr. Tuomu Suntola et al. patented the atomic layer deposition process. Through this process it became possible to deposit uniformly thin films, one atomic layer at one time. In the 1980s, nanotechnology no longer remained stochastic, but became deterministic. During this period, Dr. K. Eric Drexler advocated the significance of nanomaterials and devices.
So much of groundwork on nanotechnology made the process of production and implementation of nanomaterials relatively simple.
New Healthcare Technology and Personalized Medicines
More and more, diseases are being defined at the molecular level. Many diseases and patients’ response to medicines are influenced by the presence or absence of certain gene variants to a larger or lesser degree. Knowledge and better understanding of disease and of the genetic differences among patients is an important aspect of more personalized healthcare, which holds much potential for the future. For example, pharmacogenetics (medicines tailored to individual patients) should help develop more personalized treatments.
Personalized healthcare could bring more benefits for patients in terms of improved health outcomes, improved patient safety and reduced side-effects as well as better prescribing efficiency which will result in cost-effective practices for health services.
Much Thought Of More Innovation Friendly Regulatory Framework:
- Fosters the promises of new and emerging healthcare technology developments and personalized medicines in a responsible manner.
- Recognizes the opportunities related to evolving and emerging technologies.
- Recognizes that pharmacogenetic research and other innovative technologies must be integrated into an appropriate regulatory framework that fosters the development of treatment options, in particular of personalized healthcare.
- Promotes the application of research findings into clinical practice.
- Ensure adequate data and marketing protection for personalized medicines.
- Ensure public information and understanding of the potential benefits from these new and emerging technologies in order to avoid misinterpretations.
HURDLES OF PERSONALIZED HEALTHCARE
Only few personalized treatments are available for patients. Some of the factors hampering personalized healthcare from concept to reality are:
- The high cost of validating response-predicting molecular diagnostic tests to suitable clinical standards.
- The low reward for innovation.
- The low odds that any particular set of marker will be sufficiently sensitive and specific to justify its application in clinical practice. This makes the effort of finding meaningful biomarkers overall expensive.
New approaches and emerging health technologies, such as personalized treatment, are evolving more rapidly than legislation, leaving some areas uncovered by law or covered by outdated legislation.
NANOBIOTECHNOLOGY
Nanotechnology is widely anticipated as one of the key technologies of the 21st century. As an enabling technology, it does and will increasingly impact other technologies but also products including innovative diagnostic tools and medicines. For any technology, benefits and risks of nanotechnology have to be evaluated and will share consumers’ and patients’ interest in its safe application. Research-based biopharmaceutical companies continuously evaluate new scientific developments and innovative technologies as well as their potential application to the development of novel medicinal products. As part of the drug development process, nano-scale drug delivery systems and other nano-technology components of new medicines will undergo the same careful scrutiny that is applied to all new medicinal products with regard to both, safety and efficacy. This rigorous investigation and in-depth study applies to both preclinical and well-controlled clinical studies.
In today’s technological age, it seems advancements in all fields leap forward by the day. Medical technology certainly hasn’t been left out of the loop, and some of the breakthroughs in modern medicine have been quite revolutionary and had a huge impact. But where will the field of medicine be in 20 years from now? What major advancements are waiting just around the next corner? In this article we will consider just two of the biggest technologies that are emerging over the horizon.
Electronic Implants
We have computers everywhere these days, but it’s not just the ones on our desks that we use to surf the net. We have computer chips in washing machines and just about all of our other appliances too. In the realm of science fiction (all too often a prediction of future science) we have seen technologically enhanced humans with superhuman abilities but what if those technologies were real and used for medical purposes?
Scientists have been working for years on implementing a special kind of microchip known as a “neuroprosthetic chip” that can be implanted into the brain. This chip helps to decipher signals in the brain when the brain itself cannot, and to trigger the appropriate responses. For example, the chip could help to control epileptic seizures, or help a patient suffering with paralysis to control prosthetic limbs with thought alone.
Stem Cell Research
One of the most talked about areas of medical technology today is stem cell research. With the first human trials currently taking place to determine the safety of human treatment, stem cell technology may not be too far away. The basis of stem cell therapy is regenerative: stem cells help the body to form new cells and generate tissue. If we can harness the power of stem cells for medical use, we may be able to cure paralysis, blindness, heart disease and diabetes, treat stroke patients and repair damaged organs and tissues, helping the body to regenerate and cure itself. Some people are even optimistic that stem cell research could lead to curing cancer!
Stem cell research has been the subject of much controversy. The needed stem cells are actually taken from embryos developed using IVF techniques as there are often surplus embryos and these are donated for scientific use. The stem cells gathered in this way are generic and have no predetermined cell type, which enables scientists to force the stem cells to become a specific, needed type of cell that can be injected into a patient in need of them. The embryos are only a few days old and about the size of a full stop (period), but there are many who think that stem cell research is just plain wrong; that it is “playing God” with an unborn child. This may all change as new research shed light on the ability to use adult stem cells, but only time will tell.
Nanomedicine
Nanotechnology, especially nanomedicine, are advancing significantly day by day. Nanoparticles are being already used in many products (mainly in cosmetics), but other spheres such as pharmaceutics and general medicine are slowly applying nanotechnology standards.
Nanomedicine, along with stem cells research, will probably change the way the world sees medicine. Many experts predict that it will change everything.
This was just a brief look at what the future of medicine may hold for us, but with these and many more exciting technologies rapidly emerging that future certainly looks bright.
BIOPHARMACEUTICAL
A biopharmaceutical is defined as a medical drug (proteins including antibodies, nucleic acids, DNA, RNA or antisense oligonucleotides) which is produced using biotechnology. In the late 1990s advances in manufacturing and processing revolutionized the production of biopharmaceuticals such as recombinant DNA technology and hybridoma technology. These technological advances have enabled the market place to open up and for smaller players to enter and capitalize on the growing need for targeted, personalized medicine.
During the 1960s and 1970s formulation began to assume greater importance. More recently still, the inconvenience of parenteral administration became a focus for attempts to minimize the burden and optimize treatment. Nowadays, any development programme for a new drug will include consideration of the optimal dosage form from the conception of a drug development project. A plethora of delivery platforms have evolved to meet market demands and overcome solubility and pharmacokinetic issues, and will have an important role to play in determining the dosage form that ultimately appears on the market.
The biopharm field represents a major opportunity for generic manufacturers with sufficient resources to withstand the relatively high development costs and the technological demand. It is estimated that biosimilars, targeting the six leading biopharm products, could generate revenues in excess of $2 billion within 2-3 years. However, there are considerable challenges facing companies developing and marketing biopharm products.
Manufacturing problems will remain a significant hurdle for companies entering this field; the regulation of innovator biopharm products continues to evolve and the harmonization of regulatory processes among the three main national regulatory agencies (the EU, the US and Japan) should make life simpler for biopharm companies seeking to establish a global presence for their products.
Biotherapeutics represent 7.5 percent of all drugs on the market; they account for approximately 10 percent of the total expenditure for marketed drugs and their use is growing at more than 20 percent per year. Biotechnology drug candidates account for around 32 percent of all pipeline research programs. In addition, biological drugs are administered in life-saving or end-stage applications, 74 percent more than chemically derived pharmaceuticals.
NANOTECHNOLOGY
Nanotechnology is the science of maneuvering and modifying the structure and properties of matter at an atomic and molecular scale. Due to these manipulations, inert elements start to function as catalyst, and insoluble matter develop unique solubility capacity. Likewise, non-colloids begin exhibiting excellent colloidal properties and electrical non-conductors start conducting electricity. All these materials can be used for a vast variety of purposes in field as diverse as medicine, energy production and electronics.
In recent years, nanotechnology has found innumerable applications in the field of medicine — from drug delivery systems, nano-robots and cell repair machines to imaging, nano-particles and nano-nephrology. Owing to the extensive use of nano-materials in medical equipments and devices, nano-medicine has become a significant branch of nanotechnology. Here are some important uses of nanotechnology in the field of medicine. All these things prove that nanotechnology will play a significant role in the future, and shows why nanotechnology is useful.
Drug Delivery System And Nanoparticles
The primary objective of the drug delivery system is to make the life-saving drug available in that part of the body where it is required the most. However, most of the time, these systems fail to work efficiently because the particles of the drug are too large for the cells to absorb, or they are insoluble or they have the potential to cause tissue damage. On the other hand, due to their exceedingly small size, nanoparticles are easily taken up by the cell. Moreover, they are completely soluble and they do not also damage the tissues. In nutshell, the efficiency of the drug delivery system can be increased several times by integrating nanoparticles with them.
Coupling Of Nanoparticles With Biopharmaceuticals
Biopharmaceuticals are peptides or protein molecules that trigger multiple reactions in the human body. They are widely used in the treatment of life-threatening diseases like cancer. The effectiveness of biopharmaceuticals can be increased several times by coupling them with nanoparticles, which will proficiently deliver the peptides or proteins at the tumor site and in this manner cure cancer without causing extensive damage to the adjacent tissues and organs.
Nanotechnology And Neuro-Electronic Devices
Neuro-electronic devices are unique machines based on nanotechnology that connect the nervous system with the computer. These devices not just detect and interpret the signals from the nervous system, but also control and respond to them. They can be used in the treatment of diseases that slowly and steadily decay the nervous system like multiple sclerosis.
Nanonephrology
This is a sub-branch of nanomedicine which is concerned with the detection and treatment of kidney diseases. Here various devices based on nanotechnology are used for the studying the different kidney processes and detecting disorders. Thereafter, nanoparticles and drug delivery system are used for curing the disorder.
Nanotechnology And Cell Repair Machines
These cell repair machines use nanotechnology to penetrate into the cell and rectify disorders like DNA damage or enzyme deficiency. These machines are no bigger than a bacteria or virus.
Nanorobots
The entry of nanorobots will literally revolutionize the world of medicine. These miniature devices would not only be capable of entering into the body and detecting the diseases and infection, but they will also be capable of repairing internal injuries and wounds.
Nanotech and Cancer
Nanotechnology deals with manipulating the structure as well as properties of matter at the atomic and molecular level. As the result of this maneuvering, the properties of matter change dramatically. While some insoluble elements develop high solubility capacity, inert substances start exhibiting catalyst properties. Owning to their size and properties, nanomaterials are extensively used for the treatment of a number of diseases. Cancer is such a disease where nanotechnology can play a significant role.
Nanoparticles And Nanorobots
Cancer is a condition where changes occur in a small percentage of cells and they start replicating interminably. Problems come to the fore only when the condition becomes unmanageable. The size of nanoparticles and nanorobots is exceedingly small, and because of this property, they can easily enter into the blood vessels, organs, tissues and even the cells of the body. Additionally, they can also find out those cells that are growing abnormally. Thus, they can play a decisive role in the detection of cancer at a very early stage.
Accurate Drug Delivery
Once the cancer has been detected, it becomes essential to treat it as quickly as possible. Most of the cancer treatment methods cause widespread damage because while eliminating the cancerous cells they also start acting upon the normal cells. Drug delivery systems that use nanoparticles can effectively treat cancer without damaging the surrounding cells and tissues. These nanoparticles are smaller than the body cells, and can easily carry the drug to that part of the body where the cancerous cells are located.
Biopharmaceuticals And Cancer
Biopharmaceuticals are basically proteins molecules that trigger multiple reactions in the human body. They are widely used in the treatment of cancer. The effectiveness of these pharmaceuticals will increase several times if they are coupled with nanoparticles. The nanoparticles will carry the biopharmaceuticals directly to the tumor site without adversely affecting the cells and tissues that come in the way. In this manner, cancer would be cured and healthy cells will remain as such.
Cell Repair Machine And Cancer Treatment
Cancer primarily occurs due to mutation; the genetic information stored in the DNA is changed. As the result the affected cells divide continuously and cause the formation of tumors. The cell repair machine that is as small as a nanoparticle can easily penetrate into the cancerous cell and repair the damaged DNA. As the technique is completely non-invasive, therefore the normal cells remain unharmed.
HISTORY OF NANOTECHNOLOGY
In 1974, Norio Taniguchi of the Tokyo Science University, defined the term nanotechnology for the first time. According to his definition, nanotechnology encompasses separating, processing, consolidating and deforming matter at atomic and molecular scales. Although the term nanotechnology got its definition in 1974, the actual concept was introduced way back in 1867, when James Clerk Maxwell proposed a minuscule entity called Maxwell’s Demon that was capable of handling individual molecules.
Richard Adolf Zsigmondy was the first person to observe and measure the dimensions of nanoparticles. He was also the first person to use nanometer for characterizing the size of the nanoparticles unambiguously. He determined that 1 nm was 1/1,000,000 millimeter. He also developed the first classification system that was based on size of the particle that ranged in nanometer.
In the 20th century several developments took place that helped in characterizing nanomaterials. Like in 1920, Irving Langmuir introduced the concept of monolayer, where a layer of material is just one molecule thick. He received a Nobel Prize for this concept.
In 1959, Richard Feynman, at a meeting of American Physical Society at Caltech, put forth a process that had the ability to control and modify individual atoms and molecules. He stated that by scaling down the dimensions of the atom, dramatic changes can be brought about in its properties. After the discourse, he announced two challenges; first was the construction of nanomotor, which achieved by William McLellan in 1960,and second involved the process of scaling down the letters of Britannica Encyclopedia to fit on the head of a pin; this task was accomplished by Tom Newman in 1985.
In 1965, Gordon Moore made an astounding prediction; he stated that the number of transistors that could fit in a specific area would double every 18 years for the next 10 years. Till this date the trend is continuing, from 2000 transistors in 4004 processors to 7,000,000,000 transistors in Core 2, and Gordon’s prediction is popularly known as Moore’s Law.
In 1974, Dr. Tuomu Suntola et al. patented the atomic layer deposition process. Through this process it became possible to deposit uniformly thin films, one atomic layer at one time. In the 1980s, nanotechnology no longer remained stochastic, but became deterministic. During this period, Dr. K. Eric Drexler advocated the significance of nanomaterials and devices.
So much of groundwork on nanotechnology made the process of production and implementation of nanomaterials relatively simple.
New Healthcare Technology and Personalized Medicines
More and more, diseases are being defined at the molecular level. Many diseases and patients’ response to medicines are influenced by the presence or absence of certain gene variants to a larger or lesser degree. Knowledge and better understanding of disease and of the genetic differences among patients is an important aspect of more personalized healthcare, which holds much potential for the future. For example, pharmacogenetics (medicines tailored to individual patients) should help develop more personalized treatments.
Personalized healthcare could bring more benefits for patients in terms of improved health outcomes, improved patient safety and reduced side-effects as well as better prescribing efficiency which will result in cost-effective practices for health services.
Much Thought Of More Innovation Friendly Regulatory Framework:
- Fosters the promises of new and emerging healthcare technology developments and personalized medicines in a responsible manner.
- Recognizes the opportunities related to evolving and emerging technologies.
- Recognizes that pharmacogenetic research and other innovative technologies must be integrated into an appropriate regulatory framework that fosters the development of treatment options, in particular of personalized healthcare.
- Promotes the application of research findings into clinical practice.
- Ensure adequate data and marketing protection for personalized medicines.
- Ensure public information and understanding of the potential benefits from these new and emerging technologies in order to avoid misinterpretations.
HURDLES OF PERSONALIZED HEALTHCARE
Only few personalized treatments are available for patients. Some of the factors hampering personalized healthcare from concept to reality are:
- The high cost of validating response-predicting molecular diagnostic tests to suitable clinical standards.
- The low reward for innovation.
- The low odds that any particular set of marker will be sufficiently sensitive and specific to justify its application in clinical practice. This makes the effort of finding meaningful biomarkers overall expensive.
New approaches and emerging health technologies, such as personalized treatment, are evolving more rapidly than legislation, leaving some areas uncovered by law or covered by outdated legislation.
NANOBIOTECHNOLOGY
Nanotechnology is widely anticipated as one of the key technologies of the 21st century. As an enabling technology, it does and will increasingly impact other technologies but also products including innovative diagnostic tools and medicines. For any technology, benefits and risks of nanotechnology have to be evaluated and will share consumers’ and patients’ interest in its safe application. Research-based biopharmaceutical companies continuously evaluate new scientific developments and innovative technologies as well as their potential application to the development of novel medicinal products. As part of the drug development process, nano-scale drug delivery systems and other nano-technology components of new medicines will undergo the same careful scrutiny that is applied to all new medicinal products with regard to both, safety and efficacy. This rigorous investigation and in-depth study applies to both preclinical and well-controlled clinical studies.
Subscribe to:
Posts (Atom)
Introducing Digital PPE Matrix 2.0 – Now Voice-Activated!
๐ Introducing Digital PPE Matrix 2.0 – Now Voice-Activated! ๐ค #InnovationInSafety #PPEMatrix #HSE A question came to us: ...
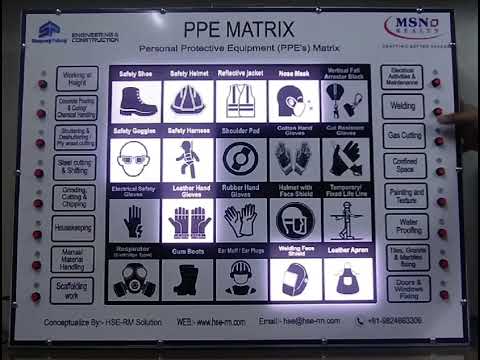
-
Chemical Safety Consciousness Sessions Chemical Safety by HSE-RM Solutions, we design customized training programs, evaluation base cert...
-
14-11-2023 Post Today Process Safety Implementation we must focuse specifically on inventory management, here are the key points to consider...
-
https://youtu.be/xydeGiZdckI Greetings, Identifying & Reporting 30th video of the series, effective recognition, Recognitio...